Oorlog staat bekend als de beste motor van vooruitgang. De tankindustrie van de Sovjet-Unie maakte in slechts enkele oorlogsjaren een duizelingwekkende kwalitatieve sprong. De echte kroon hierop waren de tanks van de IS-serie.
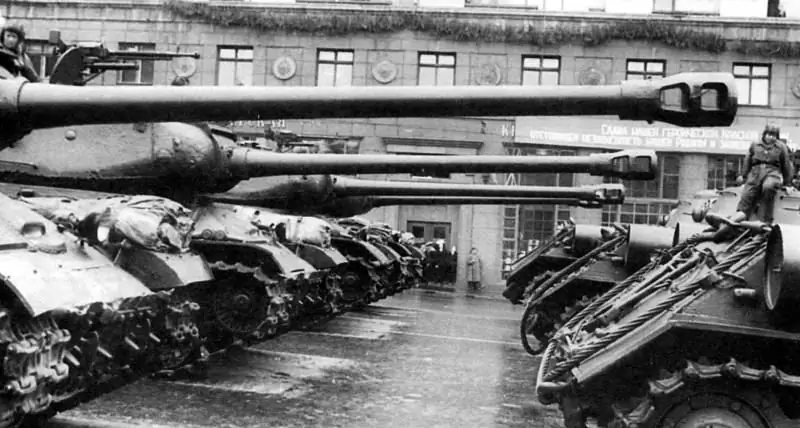
Magnitogorsk recepten
In het vorige deel van het verhaal ging het over het 70L hoge hardheid gegoten pantser dat werd gebruikt voor de torentjes van de IS-tanks. De pantserontwikkelaars van TsNII-48 waren verre van de eerste ervaring met het creëren van bescherming voor zware tanks.
Vóór de Koersk Ardennen, die een katalysator werd voor de ontwikkeling van de bouw van zware tanks voor huishoudelijk gebruik, was het belangrijkste doel van modernisering de KV-tank. Aanvankelijk waren alle werkzaamheden gericht op het verminderen van het aandeel schaarse legeringsadditieven in de samenstelling van het pantser. Zelfs de naam in TsNII-48 kwam met een passende naam - economisch gelegeerd staal. Het originele pantser van het merk FD-7954, waarmee de KV-tank de Grote Patriottische Oorlog binnenging, bevatte volgens de technische vereisten tot 0,45% molybdeen, 2,7% nikkel en chroom.
Tegen het einde van 1941 creëerde een groep onderzoekers onder leiding van Andrei Sergejevitsj Zavyalov van het Gepantserde Instituut een recept voor staal FD-6633 of 49C, waarin molybdeen niet meer dan 0,3% nodig had, chroom - tot 2,3% en nikkel - tot 1,5%. Aangezien de tanks van de KV-serie uit de tweede helft van 1941 tot 1943 ongeveer 4.000 exemplaren werden verzameld, kan men zich de hoeveelheid echte besparingen bij het legeren van metalen voorstellen.
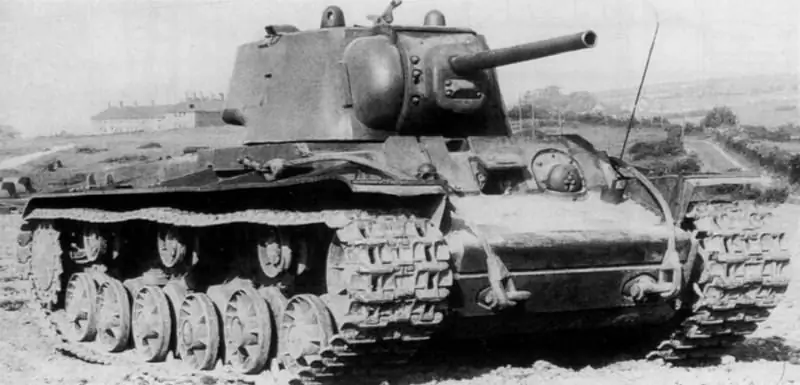
Het geheim van succes
Het geheim van het succes van de metallurgen ligt in de studie van de parameters van de vorming van vezelige pantserbreuken - de belangrijkste parameter van projectielweerstand. Het bleek dat je een aanzienlijk deel van de legeringselementen kunt missen door simpelweg de afkoelsnelheid van het pantser tijdens het afschrikken te veranderen. Maar dit is eenvoudig in woorden - hoeveel voorbereidende experimenten en smeltmetallurgen moesten doen, alleen de nu geclassificeerde archieven zullen kunnen vertellen.
In de Magnitogorsk Metallurgical Plant in 1941 werden de eerste prototypes van 49C-staal verkregen, die niet onderdoen voor het traditionele "vooroorlogse" pantser. Met name de beschietingen door het 76 mm kanon toonden volledige overeenstemming met de tactische vereisten voor de tank. En sinds 1942 werd alleen pantser met de naam 49C gebruikt voor de KV-serie. Het is de moeite waard eraan te denken dat het verbruik van chroom, molybdeen en nikkel aanzienlijk is afgenomen.
De zoektocht naar nieuwe formuleringen van bepantsering voor zwaar materieel eindigde daar niet. In 1942 werd staal GD-63-3 "gelast", volledig verstoken van schaars chroom en nikkel. Tot op zekere hoogte werd nikkel vervangen door mangaan - het aandeel ervan nam meer dan drie keer toe (tot 1,43%). Prototypes van het nieuwe pantser werden beschoten. En ze bleken best geschikt voor massaal gebruik in het ontwerp van de KV. Maar de Klim Voroshilov-tanks met een middelhard pantser gingen met pensioen. En de plaats van zware voertuigen werd ingenomen door "Joseph Stalin" -voertuigen met een zeer hard pantser.
Gerold pantser 51C
Als het 70L-pantser voor de IS-2-toren kon worden gegoten, werkte deze truc niet met de rompdelen van de tank. Hier werden ingenieurs geconfronteerd met twee problemen tegelijk: het creëren van een zeer hard pantser van grote dikte en de noodzaak om het in een afgewerkte romp te lassen.
Iedereen die geïnteresseerd is, is waarschijnlijk al op de hoogte van de problemen die worden veroorzaakt door het lassen van het T-34-pantser - er is een grote kans op scheuren op het gebied van lassen. De IS-2 was geen uitzondering. En zijn lichaam moest oorspronkelijk worden gekookt van uiteindelijk met warmte behandelde delen.
De TsNII-48-specialisten realiseerden zich welke moeilijkheden en gevaren een dergelijke technologische oplossing met zich mee zou brengen bij militaire operaties en veranderden de tankproductiecyclus. Als gevolg hiervan werd in 1943, in de Ural Heavy Machine Building Plant en de Chelyabinsk Plant No. 200, besloten om de IS-2-romp te koken van pantserplaten die na het rollen slechts een hoge vakantie hadden doorstaan. Dat wil zeggen, in feite was de romp van een zware tank samengesteld uit "ruw" staal. Dit verminderde de lasdefecten op het 51C-gewalste pantser met hoge hardheid aanzienlijk.
De laatste warmtebehandeling door verwarming vóór afschrikken werd al op het gelaste lichaam van de tank uitgevoerd, nadat het eerder was versterkt met interne stutten. Het lichaam werd drie uur in de oven bewaard. En toen, op speciale apparaten, werden ze overgebracht naar een waterafschriktank en daarin gedurende 15 minuten bewaard. Bovendien steeg de watertemperatuur in de blustank van 30 naar 55°C. De oppervlaktetemperatuur van het lichaam na verwijdering uit het water was 100-150 °. En dat is niet alles.
Na het afschrikken werd het lichaam onmiddellijk onderworpen aan lage tempering in een circulatieoven bij een temperatuur van 280-320 ° met vasthouden na het bereiken van deze temperatuur gedurende 10-12 uur. De lage tempering van gegoten torens van 70L-pantser werd op een vergelijkbare manier uitgevoerd. Interessant is dat de scheurcontrole in de experimentele IS-2-rompen vier maanden duurde, toen de eerste productietanks de fabriekspoorten verlieten.
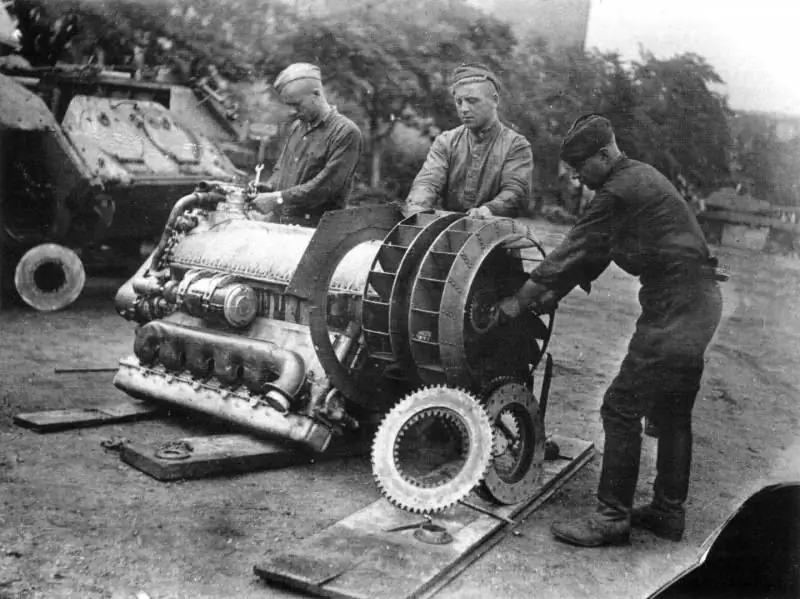
Chemische samenstelling
Wat was het 51C-rolpantser dat de belangrijkste werd voor de IS-2, ISU-122 en ISU-152? Het is een diephardend staal voor grote pantserdiktes met de volgende chemische samenstelling (%):
C0, 18-0, 24
Mn 0, 70-1, 0
Si 1, 20-1, 60
Cr 1, 0-1, 5
Ni 3.0-3.8
Ma 0, 20-0, 40
P ≤0.035
S ≤0.035.
In vergelijking met het gegoten pantser 70L had het 51C-gewalste staal een hoger gehalte aan molybdeen en nikkel, wat een toename van de hardbaarheid tot 200 mm garandeerde. Toen de rompen van zware tanks werden afgevuurd met 88 mm-granaten, bleek dat het pantser van hoge hardheid veel beter was in duurzaamheid dan zijn voorgangers met gemiddelde hardheid. De kwestie van het plaatsen van gerold pantser 51C werd onmiddellijk opgelost.
Slim lassen
Een belangrijke bijdrage aan het succes van de ontwikkeling van pantserproductie van tanks van de IS-serie werd geleverd door automatisch lassen van staal onder een laag flux. Omdat het begin 1944 onmogelijk was om het hele proces van het vervaardigen van een gepantserde tankromp op dergelijk lassen over te dragen, concentreerden de ingenieurs zich op het automatiseren van de meest uitgebreide en mechanisch belaste naden.
In fabriek nr. 200 in Chelyabinsk, tijdens het assembleren van de romp van de IS-2 zware tank, kon slechts 25% van alle lassen worden geautomatiseerd. Medio 1944 was Tankograd in staat om 18% van alle mogelijke 25% van de lassen te automatiseren. De totale lengte van de lasnaden langs de romp van de IS-2 zware tank was 410 strekkende meter, waarvan 80 strekkende meter werd uitgevoerd door de geautomatiseerde lasmethode.
Dit resultaat heeft geleid tot aanzienlijke besparingen op schaarse hulpbronnen en elektriciteit. Het was mogelijk om tot 50 gekwalificeerde handlassers vrij te maken (hun arbeidskosten bedroegen 15.400 manuren) en 48.000 kilowattuur elektriciteit te besparen. Verminderd verbruik van elektroden (ongeveer 20.000 kg, austenitisch - 6.000 kg), zuurstof (met 1.440 kubieke meter).
De tijd die aan het lassen wordt besteed, is ook aanzienlijk verminderd. Het lassen van de bodem en de torenkast aan de zijkanten met een naad van zestien meter kostte bijvoorbeeld 9,5 manuren in handmatige modus, en slechts 2. Een naad van vergelijkbare lengte die de bodem met de zijkanten van de tankromp verbindt in automatische modus vereist 3 manuren (in handleiding direct 11, 4). Tegelijkertijd zouden hoogopgeleide lassers kunnen worden vervangen door ongeschoolde werknemers in automatisch lassen.
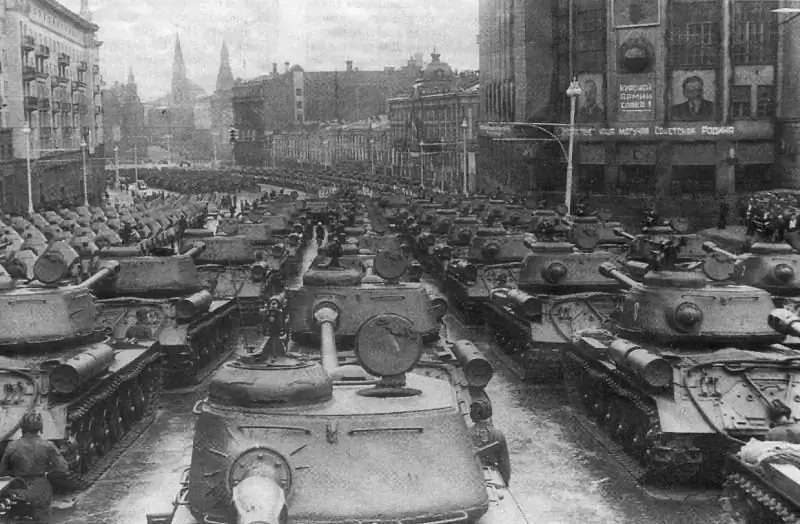
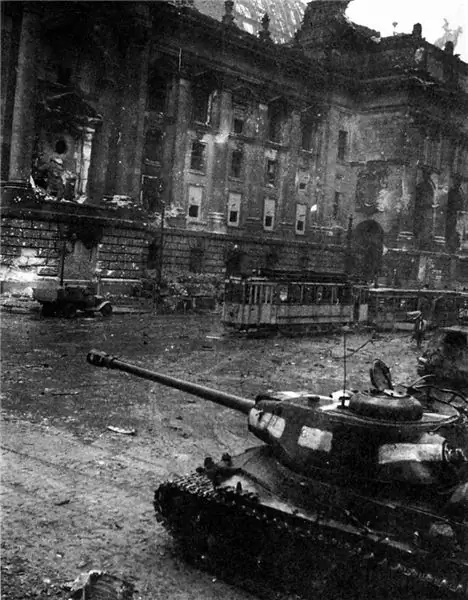
Oeral SAG's
Onderzoeker van de Sovjet-tankindustrie, kandidaat voor historische wetenschappen Zapariy Vasily Vladimirovich van het Instituut voor Geschiedenis en Archeologie van de Oeral-afdeling van de Russische Academie van Wetenschappen beschrijft in een van zijn werken in detail de automatische laseenheden die in de Oeral worden gebruikt voor gepantserde romp productie.
De meest voorkomende was een aanvalsgeweer van het type "ACC" met een Bushtedt-kop. Er waren acht van dergelijke installaties in Uralmash. De draadaanvoersnelheid in deze machine was afhankelijk van de spanning in de boog. Er waren 5 eenheden nodig, waaronder 3 kinematische elektromotoren en 1 motor-generator.
Halverwege 1943 werd de SA-1000-lasmachine ontworpen voor de behoeften van de IS-2 zware tanks. Of een lasapparaat met een capaciteit tot 1000 A.
Om de productie van gepantserde rompen voor de nieuwe zware tank IS-3 van Chelyabinsk onder de knie te krijgen, ontwierpen de ingenieurs van de fabriek in 1944 het apparaat "SG-2000". Deze machine is ontworpen om te werken met koolstofarme lasdraden met een grotere diameter (6-8 mm) en vond zijn toepassing bij de vervaardiging van de IS-3-toren. De installatie had een dispenser om een speciale samenstelling (verschillende ferrolegeringen) in het lasgedeelte te brengen om het daarin aanwezige metaal te deoxideren (herstellen). In totaal werden op het principe van zelfregulering van de lasboog bij UZTM tegen 1945 9 automatische lasinstallaties van drie typen gecreëerd: "SA-1000", "SG-2000", "SAG" ("Automatisch lassen hoofd").
Mooier dan Duits pantser
Het resultaat van het hele verhaal met de bepantsering van zware IS-tanks was een verrassend snelle ontwikkeling van een stalen recept dat het Duitse pantser overtrof in zijn tactische eigenschappen. TsNII-48 kreeg een hardbaar 120 mm staal, waarvan de dikte, indien nodig, kon worden vergroot tot 200 mm.
Dit werd de belangrijkste basis voor de ontwikkeling van de naoorlogse familie van zware Sovjettanks.