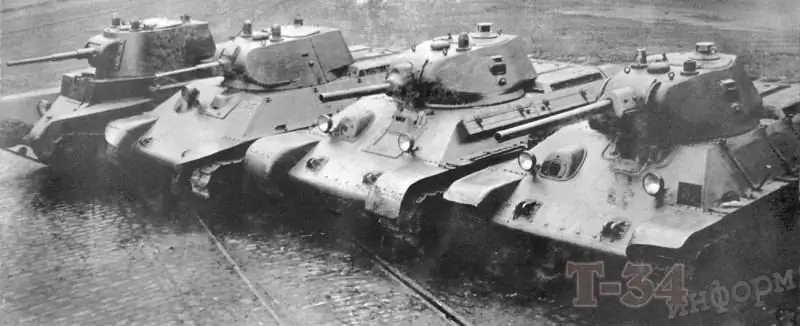
Wachten op de oorlog
Problemen met de tankproductie in de Sovjet-Unie in de jaren 1920 en 1930, voornamelijk in verband met de onbeschikbaarheid van de industrie, werden gedeeltelijk verklaard door de achterstand van de pantserindustrie. Aan het begin van 1932 konden slechts twee van de geplande vier ondernemingen bepantsering smelten en walsen. Dit waren de fabrieken van Izhora en Mariupol. Door de te hoge eisen aan de productiesnelheid (dit was een teken van die tijd) liepen deze fabrieken chronisch achter op de plannen. Dus bij een van de oudste ondernemingen in het land, de Izhora-fabriek in de stad Kolpino, konden ze in een jaar slechts 38% van het plan beheersen, en in Mariupol in de Iljitsj-fabriek - slechts een kwart. Dit was grotendeels te danken aan de productie van complexe gecementeerde heterogene bepantsering, die ze sinds 1910 in ons land wisten te maken. Een soortgelijk type pantser was nodig om bestand te zijn tegen scherpe projectielen en kogels, die de gebruikelijke homogene gemiddelde en lage hardheid niet opleverden. In die tijd was gecementeerde bepantsering verdeeld in twee klassen: laaggehard eenzijdig gecementeerd met een voldoende harde achterkant en, in de tweede versie, met een middelharde achterkant. Kortom, voor de productie van dergelijke "sandwiches" was chroom-molybdeen en chroom-nikkel-molybdeenstaal nodig, waarvoor schaarse geïmporteerde ferrolegeringsadditieven nodig waren. Het belangrijkste legeringselement van deze staalsoorten was chroom (1, 5-2, 5%), dat intensieve carbonisatie bevordert en het bereiken van een hoge hardheid van de gecementeerde laag na afschrikken. Een poging om binnenlands mangaan en silicium te gebruiken voor gehard staal in plaats van geïmporteerd chroom leverde een negatief resultaat op. Wanneer gelegeerd met mangaan, werd onthuld dat het staal gevoelig is voor korrelgroei bij de carboneringstemperatuur (920-950 graden Celsius), vooral bij lange blootstellingen die nodig zijn om tot grote diepte te carboneren. Correctie van de tijdens het cementeren oververhitte gecarboniseerde laag leverde aanzienlijke problemen op en ging gepaard met de noodzaak om meervoudige herkristallisatie toe te passen, wat een aanzienlijke ontkoling van de gecementeerde laag en plaatgeleiders veroorzaakte, en ook economisch onrendabel was. Niettemin werd tot het begin van de jaren '30 gecementeerde bepantsering zowel in de luchtvaart als in de tankbouw gebruikt. In vliegtuigen werden pantserplaten tot 13 mm dik gecementeerd, zoals tankpantsers tot 30 mm. Er waren ook ontwikkelingen van kogelwerend 20 mm gecementeerd pantser, dat niet verder ging dan experimentele ontwikkeling. Een dergelijk pantser moest absoluut enorm zijn, wat alleen gigantische middelen vereiste voor de ontwikkeling van de productie.
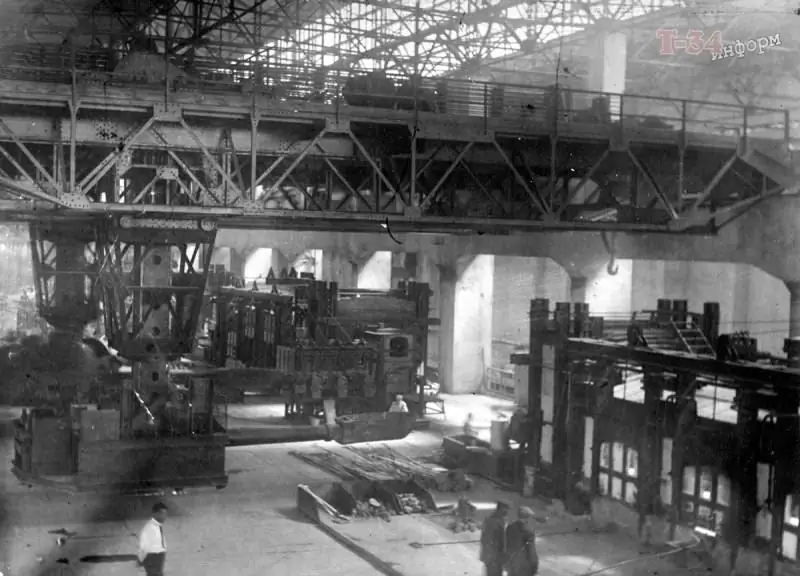
Ondanks dergelijke problemen bij de productie van gecementeerd pantser, was de romp van de T-28-tank er bijna volledig van gemaakt. Maar geleidelijk aan verliet de binnenlandse industrie de technologieën voor het cementeren van pantserplaten, grotendeels als gevolg van de extreem hoge uitval. Gezien de productieplannen die door de regering en de gespecialiseerde volkscommissariaten werden geëist, was dit helemaal niet verwonderlijk. De Izhora-fabriek was de eerste die overschakelde naar het nieuwe pantser, nadat hij het smelten van hooghard chroom-kiezelachtig-mangaanpantser "PI" onder de knie had. In Mariupol beheersten ze het heterogene mangaan "MI". Het land stapte geleidelijk over naar zijn eigen ervaring in het ontwerpen van pantsers. Tot die tijd was het gebaseerd op buitenlandse technologieën (voornamelijk Brits). De weigering om het pantser te cementeren maakte de platen dikker met dezelfde pantserweerstand. Dus in plaats van 10 en 13 mm gecementeerde bepantsering, moest de T-26-romp worden gelast uit 15 mm-platen van Izhora-staal "PI". In dit geval was de tank 800 kilogram zwaar. Opgemerkt moet worden dat de overgang van duur gecementeerd staal naar relatief goedkope homogene pantsertechnologieën zeer nuttig bleek in oorlogstijd. Als dit niet in de vooroorlogse jaren was gebeurd, zou de ontwikkeling van het smelten en walsen van dure soorten pantser onwaarschijnlijk zijn geweest, gezien de evacuatie van bedrijven in 1941-1942.
Sinds de vooroorlogse jaren werd de hoofdrol bij het zoeken en onderzoeken van nieuwe soorten pantser gespeeld door het "Armor Institute" TsNII-48, dat nu bekend staat als het NRC "Kurchatov Institute" - TsNII KM "Prometheus". Het TsNII-48-team van ingenieurs en wetenschappers bepaalde de belangrijkste richtingen van de binnenlandse wapenindustrie. In het laatste decennium voor de oorlog werd het verschijnen in het buitenland van pantserdoordringende artillerie met kalibers van 20 tot 50 mm een serieuze uitdaging. Dit dwong de ontwikkelaars om op zoek te gaan naar nieuwe recepten voor het koken van tankpantsers.
Geboorte van 8C
Vervang gecementeerde bepantsering die bestand is tegen scherpe projectielen en kogels op lichte en middelzware gepantserde voertuigen alleen door staal met een hoge hardheid. En dit werd met succes beheerst door binnenlandse metallurgen. Romp van gepantserde voertuigen BA-10, lichte tanks T-60 (pantserdikte 15 mm, frontaal - 35 mm), T-26 (pantserdikte 15 mm) en natuurlijk middelgrote tanks T-34 (pantserdikte 45 mm). De Duitsers hadden ook een hoge hardheidspantser een prioriteit. In feite werden alle bepantsering (beginnend met infanteriehelmen en eindigend met beschermende constructies voor de luchtvaart) uiteindelijk van hoge hardheid, ter vervanging van de gecementeerde. Misschien konden alleen zware KV's zich een middelhard pantser veroorloven, maar dit moest worden betaald met de grotere dikte van de platen en de uiteindelijke massa van de tank.
Het 8C-pantserstaal, de basis van de anti-kanonverdediging van de T-34-tank, werd een echte kroon van creativiteit van binnenlandse metallurgen. Opgemerkt moet worden dat de productie van 8C-pantser in de vooroorlogse jaren en tijdens de Grote Patriottische Oorlog twee serieus verschillende processen waren. Zelfs voor de vooroorlogse industrie van de Sovjet-Unie was de productie van 8C een complex en duur proces. Ze konden het alleen in Marioepol met succes beheersen. De chemische samenstelling van 8C: C - 0,22-0,28%, Mn - 1,0-1,5%, Si - 1,1-1,6%, Cr - 0,7-1,0%, Ni - 1,0-1,5%, Mo - 0,15-0,25%, P - minder dan 0,035% en S - minder dan 0,03%. Voor het smelten waren openhaardovens met een capaciteit tot 180 ton nodig, waardoor toekomstige bepantsering in relatief kleine mallen van 7, 4 ton elk werd gegoten. Deoxidatie van de vloeibare legering (verwijdering van overtollige zuurstof) in de oven werd uitgevoerd in een kostbare diffuse methode met koolstof of silicium. De afgewerkte ingot werd uit de vorm gehaald en gerold, gevolgd door langzame afkoeling. In de toekomst werd het toekomstige pantser opnieuw verwarmd tot 650-680 graden en gekoeld in de lucht: het was een hoge vakantie, ontworpen om het staal plasticiteit te geven en de kwetsbaarheid te verminderen. Pas daarna was het mogelijk om de staalplaten mechanisch te bewerken, omdat de daaropvolgende harding en lage tempering bij 250 graden het te hard maakte. Na de laatste uithardingsprocedure met 8C was het zelfs moeilijk om iets anders te doen dan de carrosserie eruit te lassen. Maar ook hier waren er fundamentele moeilijkheden. Aanzienlijke interne lasspanningen als gevolg van de lage ductiliteit van het 8C-pantsermetaal, vooral met zijn lage kwaliteit, leidend tot de vorming van scheuren, die in de loop van de tijd vaak toenemen. Scheuren rond de naden kunnen zelfs 100 dagen nadat de tank is vervaardigd, ontstaan. Dit werd tijdens de oorlog een echte plaag van de tankbouw van de Sovjet-Unie. En in de vooroorlogse periode was de meest effectieve manier om de vorming van scheuren tijdens het lassen van 8C-pantser te voorkomen, het gebruik van voorlopige lokale verwarming van de laszone tot een temperatuur van 250-280 graden. Voor dit doel ontwikkelde TsNII-48 speciale inductoren.
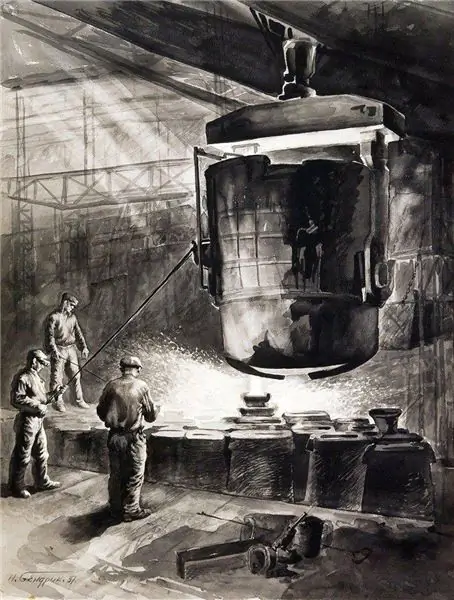
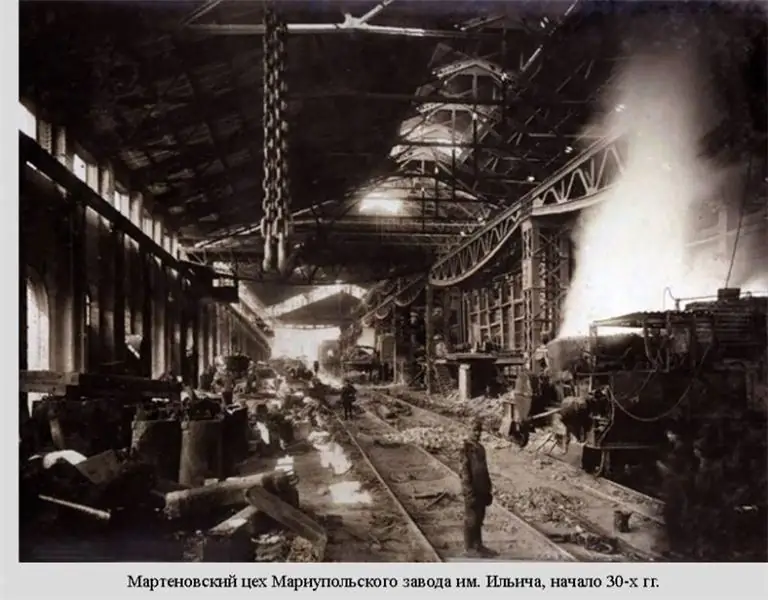
8C was niet de enige staalsoort voor T-34 bepantsering. Waar de kans zich voordeed, werd die ingeruild voor andere, goedkopere rassen. In de vooroorlogse periode ontwikkelde TsNII-48 2P structurele bepantsering, waarvan de productie aanzienlijk energie bespaarde en het rollen van platen vereenvoudigde. De chemische samenstelling van 2P: C - 0,23-0,29%, Mn - 1,2-1,6%, Si - 1,2-1,6%, Cr - minder dan 0,3%, Ni - minder dan 0,5%, Mo - 0,15-0,25%, P - minder dan 0,035% en S - minder dan 0,03%. Zoals u kunt zien, waren de belangrijkste besparingen in schaars nikkel en chroom. Tegelijkertijd bleven zeer krappe toleranties voor de aanwezigheid van fosfor en zwavel onveranderd voor 2P, wat natuurlijk moeilijk te bereiken was, vooral in oorlogstijd. Ondanks alle vereenvoudigingen onderging structurele bepantsering van 2P-staal nog steeds een warmtebehandeling - afschrikken en hoge tempering, die de thermische apparatuur die nodig is voor de warmtebehandeling van meer kritische pantseronderdelen van tanks aanzienlijk belast, en ook de productiecyclus aanzienlijk verhoogde. Tijdens de oorlog waren TsNII-48-specialisten in staat technologieën te ontwikkelen voor het verkrijgen van vergelijkbaar staal, waarvan de productie middelen vrijmaakte voor het 8C-hoofdpantser.