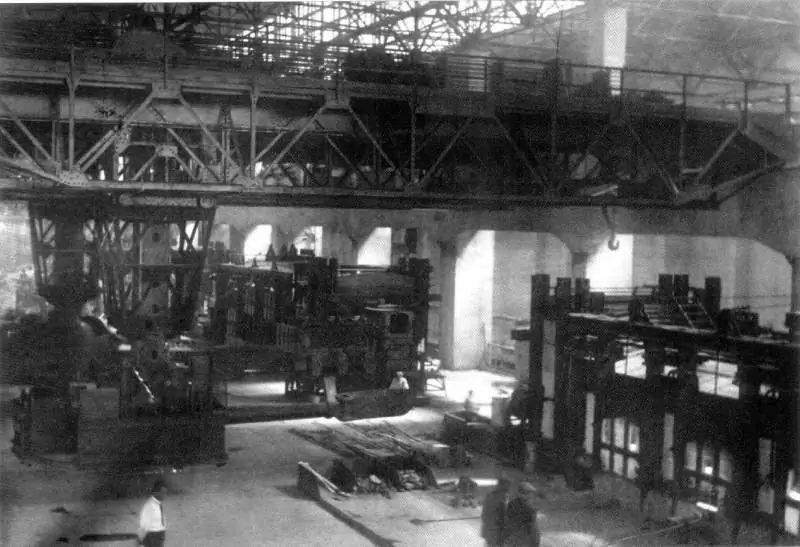
Strategische hulpbron
Het is moeilijk om de productie van hoogwaardig staal voor het militair-industriële complex in oorlogssituaties te overschatten. Dit is een van de belangrijkste factoren voor het succes van legers op het slagveld.
Zoals u weet, behoorden de metallurgen van Krupp tot de eersten die leerden hoe ze hoogwaardig staal van wapenkwaliteit konden produceren.
Aan het einde van de 19e eeuw namen de Duitsers het Thomas-productieproces over. Deze manier van staalsmelten maakte het mogelijk om fosforverontreinigingen uit het erts te verwijderen, wat automatisch de kwaliteit van het product verhoogde. Hoogwaardig pantser en wapenstaal zorgden tijdens de Eerste Wereldoorlog vaak voor de superioriteit van de Duitsers op het slagveld.
Om een dergelijke productie te organiseren, waren nieuwe vuurvaste materialen nodig, die de binnenoppervlakken van de ovens bekleedden. De Duitsers gebruikten de nieuwste vuurvaste materialen van magnesiet voor hun tijd, bestand tegen temperaturen van meer dan 2000 graden. Dergelijke stoffen met een hogere vuurvastheid zijn gebaseerd op magnesiumoxiden met kleine mengsels van aluminiumoxiden.
Aan het begin van de 20e eeuw konden landen met technologieën voor de massaproductie van vuurvaste materialen van magnesiet het zich veroorloven hoogwaardige bepantsering en geweerlopen te produceren. Dit is te vergelijken met een strategisch voordeel.
Lager in termen van brandwerendheid waren de zogenaamde zeer vuurvaste materialen die bestand zijn tegen temperaturen van 1750 tot 1950 graden. Dit zijn vuurvaste materialen van dolomiet en aluminiumoxide. Vuurvaste materialen van vuurvaste klei, halfzuur, kwarts en dinas zijn bestand tegen temperaturen van 1610 tot 1750 graden.
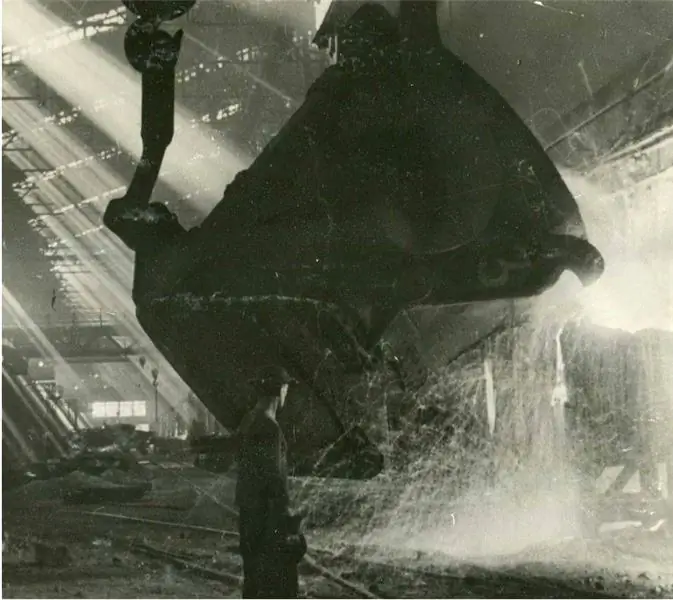
Trouwens, technologieën en locaties voor de productie van vuurvaste materialen van magnesiet verschenen voor het eerst in Rusland in 1900.
Satka magnesiet vuurvaste baksteen in 1905 werd bekroond met een gouden medaille op de World Industrial Exhibition in Luik. Het werd geproduceerd in de buurt van Chelyabinsk in de stad Satka, waar zich een unieke magnesietafzetting bevond.
Het periklaasmineraal, waarvan de vuurvaste materialen in de fabriek werden gemaakt, was van hoge kwaliteit en behoefde geen extra verrijking. Als gevolg hiervan was het vuurvaste magnesiet van Satka superieur aan zijn tegenhangers uit Griekenland en Oostenrijk.
Overbruggen van de kloof
Ondanks de vrij hoogwaardige magnesietbaksteen van Satka, waren tot de jaren '30 de belangrijkste vuurvaste materialen van Sovjet-metallurgen dinas-materialen uit klei. Natuurlijk lukte het niet om een hoge temperatuur te krijgen voor het smelten van staal van wapenkwaliteit - de bekleding van de binnenkant van openhaardovens brokkelde af en vereiste buitengewone reparaties.
Er was niet genoeg Satka-steen en in de postrevolutionaire periode gingen de belangrijkste productietechnologieën verloren.
Tegelijkertijd gingen de Europeanen door - het Oostenrijkse Radex-magnesiet onderscheidde zich bijvoorbeeld door uitstekende brandwerendheid.
De Sovjet-Unie kocht dit materiaal. Maar het was onmogelijk om een analoog te krijgen zonder een productiegeheim. Dit probleem werd opgepakt door een afgestudeerde van de Technische Staatsuniversiteit van Moskou. N. E. Bauman Alexey Petrovitsj Panarin. Bij de Magnet-fabriek (voorheen de Satka Combine) leidde hij in 1933 het Central Plant Laboratory. En vijf jaar later lanceerde hij de massaproductie van periklaas-chromiet of chromomagnesiet vuurvaste materialen voor open haardovens.
In de Zlatoust Metallurgical Plant en de Moscow Hammer and Sickle verving Panarins vuurvaste materialen de verouderde dina's.
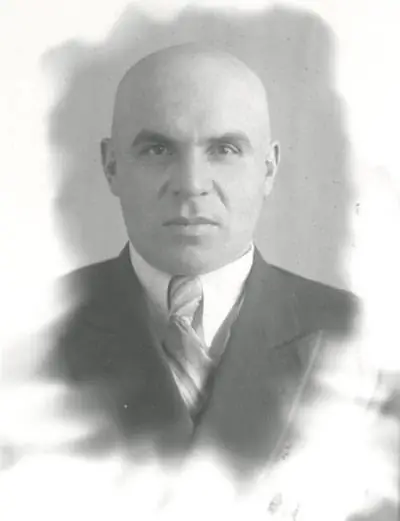
De technologie, die al enkele jaren in het laboratorium van "Magnezit" was ontwikkeld, bestond uit een speciale samenstelling en deeltjesgrootte.
Voorheen produceerde de fabriek conventionele chroom-magnesietstenen, bestaande uit magnesiet en chroomijzererts, in een verhouding van 50/50. Het geheim dat door de groep van Panarin werd onthuld, was als volgt:
“Als chromieterts in grove granulometrische korrels met een minimaal gehalte aan fracties kleiner dan 0,5 mm wordt toegevoegd aan een gewone magnesietlading, dan neemt zelfs bij 10% toevoeging van dergelijk erts de thermische stabiliteit van de steen sterk toe.
Naarmate de toevoeging van chromieterts van grove granulometrie toeneemt, groeit de stabiliteit van de steen en bereikt deze een maximum bij een bepaalde verhouding van componenten."
Chromiet voor het nieuwe vuurvaste materiaal werd gewonnen in de Saranovskoye-mijn en periklaas werd voortgezet in Satka.
Ter vergelijking: een gewone "pre-revolutionaire" magnesietsteen was bestand tegen temperaturen die 5-6 keer lager waren dan de nieuwigheid van Panarin.
In de kopersmeltfabriek in Kirovograd weerstond chroom-magnesiet vuurvast materiaal in het dak van een galmoven gedurende 151 dagen temperaturen tot 1550 graden. Voorheen moesten vuurvaste materialen in dergelijke ovens elke 20-30 dagen worden vervangen.
Tegen 1941 was de productie van grootschalige vuurvaste materialen onder de knie, waardoor het mogelijk werd om de materialen te gebruiken in grote staalovens bij temperaturen tot 1800 graden. Een belangrijke bijdrage hieraan werd geleverd door de technisch directeur van "Magnezit" Alexander Frenkel, die een nieuwe methode ontwikkelde om het vuurvaste materiaal op de daken van de ovens te bevestigen.
Vuurvaste materialen voor de overwinning
Eind 1941 bereikten de metallurgen van Magnitka het voorheen ondenkbare - voor het eerst in de geschiedenis beheersten ze het smelten van pantserstaal voor T-34-tanks in de belangrijkste zware openhaardovens.
De belangrijkste leverancier van vuurvaste materialen voor zo'n belangrijk proces was Satka "Magnezit". Het is onnodig om te praten over de moeilijkheden van oorlogstijd, toen een derde van de fabrieksarbeiders naar het front werd geroepen en de staat eiste dat het plan te vol werd uitgevoerd. Niettemin deed de fabriek zijn werk, en Panarin in 1943
"Voor het beheersen van de productie van zeer vuurvaste producten uit lokale grondstoffen voor ferrometallurgie"
werd bekroond met de Stalinprijs.
In 1944 zal deze metallurg-onderzoeker een technologie ontwikkelen voor de productie van hoogwaardig magnesietpoeder "Extra". Dit halffabrikaat werd gebruikt om een geperst vuurvast materiaal te bereiden dat wordt gebruikt bij de bijzonder belangrijke productie van gepantserd staal in elektrische ovens. De temperatuurlimiet voor dergelijke vuurvaste materialen bereikte 2000 graden.
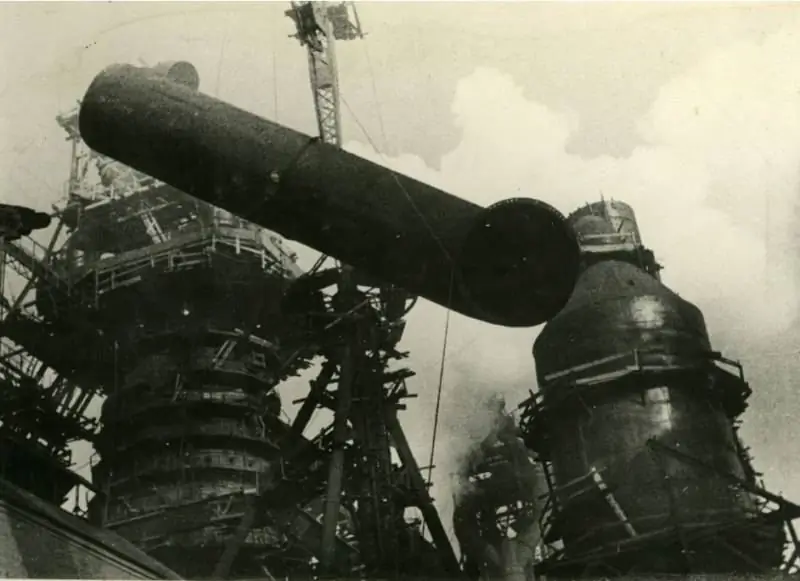
Maar men moet er niet van uitgaan dat het voorbeeld van een over het algemeen succesvolle Magnezit-fabriek zich uitstrekte tot de gehele vuurvaste industrie van de Sovjet-Unie.
Een bijzonder moeilijke situatie ontwikkelde zich in de Oeral, waar in 1941-1942 vrijwel het hele tankgebouw van het land werd geëvacueerd.
De metallurgische fabrieken Magnitogorsk en Novotagilsk werden geheroriënteerd op de productie van bepantsering en leverden producten aan Sverdlovsk Uralmash, Chelyabinsk "Tankograd" en Nizhny Tagil tankfabriek nr. 183. Tegelijkertijd hadden metallurgische fabrieken hun eigen productie van vuurvaste materialen uit lokale grondstoffen.
In Magnitka produceerde de dinas-chamottefabriek bijvoorbeeld 65-70 duizend ton bakstenen per jaar. Dit was zelfs niet genoeg voor hun eigen behoeften, om nog maar te zwijgen van de leveringen aan andere ondernemingen.
De eerste moeilijkheden ontstonden toen tankfabrieken hun eigen verwarmings- en thermische ovens begonnen te bouwen. Ural-metallurgie had al nauwelijks genoeg vuurvaste materialen, en toen vereiste de rompproductie van tankfabrieken hoogwaardige materialen voor het bekleden van de ovens.
Er was hier geen sprake van vuurvaste chromomagnesiet - dit materiaal was schaars en werd zelfs geëxporteerd in ruil voor American Lend-Lease. Dit wordt in ieder geval in een aantal bronnen vermeld. Oeral-historici schrijven dat het dure chromomagnesite van Panarin naar het buitenland zou kunnen gaan in ruil voor schaarse ijzerlegeringen voor tankbepantsering. Maar daar is nog geen direct bewijs voor.
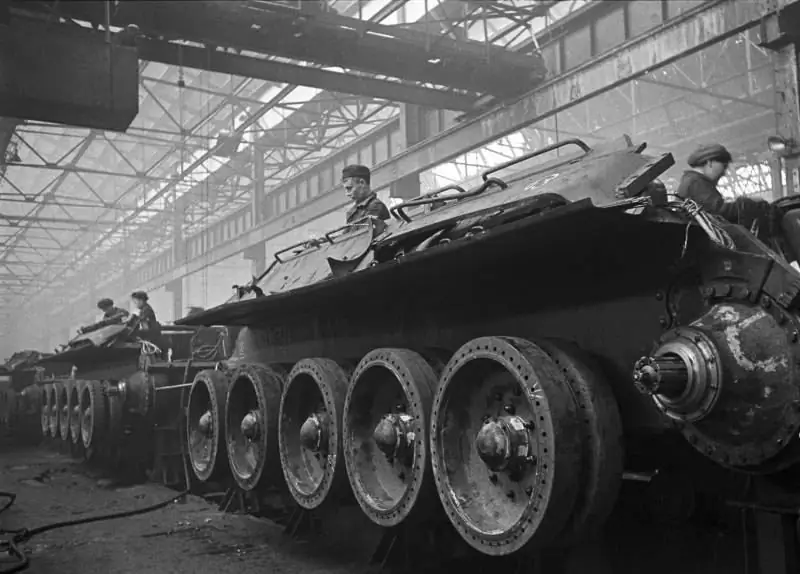
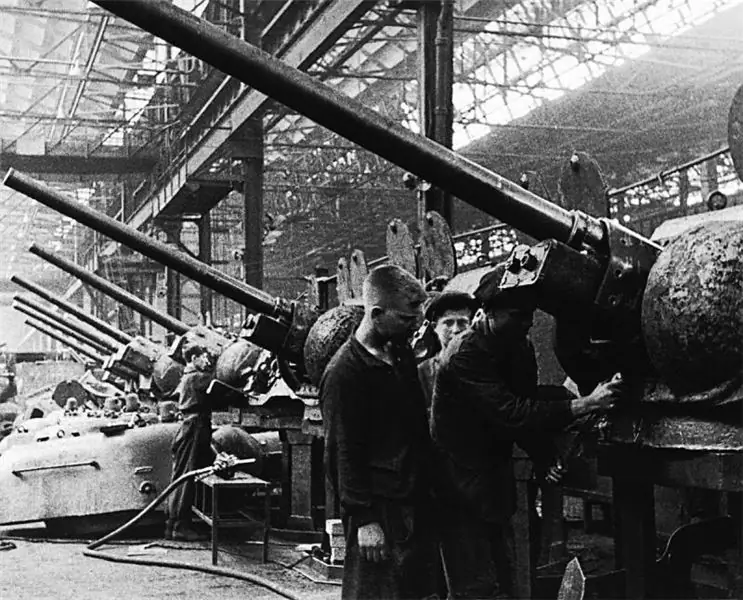
Tankfabrieken vertrouwden meestal op vuurvast materiaal van dinas, geproduceerd door de fabriek in Pervouralsk. Maar ten eerste werd er slechts 12 duizend ton per maand geproduceerd, en ten tweede namen metaalbewerkers het leeuwendeel.
De uitbreiding van de productie in de fabriek in Pervouralsk verliep erg traag. En tegen het midden van 1942 verschenen er slechts 4 nieuwe ovens. De rest was ofwel niet klaar, of bestond over het algemeen alleen in projecten.
Vuurvaste materialen voor openhaarden van tankfabrieken waren vaak van slechte kwaliteit, niet volledig en op het verkeerde moment. Alleen voor de reparatie van Uralmash-ovens in het vierde kwartaal van 1942 was 1035 ton brandwerende stenen nodig en werd slechts ongeveer 827 ton ontvangen.
In 1943 stopte de openhaardwinkel van Uralmash in het algemeen bijna vanwege het gebrek aan vuurvaste materialen voor reparatie.
De kwaliteit van de tijdens de oorlog geleverde vuurvaste materialen liet veel te wensen over. Als de dinas-steen van de openhaardoven onder normale omstandigheden 400 hitte zou kunnen weerstaan, dan overschreed het in oorlogstijd niet meer dan 135 hittes. En in maart 1943 was deze parameter gedaald tot 30-40 heats.
Deze situatie toont duidelijk aan hoe het gebrek aan één hulpbron (in dit geval vuurvaste middelen) het werk van de hele defensie-industrie ernstig kan vertragen. Zoals de kandidaat voor historische wetenschappen Nikita Melnikov in zijn werken schrijft, stopten in maart 1943 drie openhaardovens van Uralmash nog steeds en voerden een volledige cyclus van reparatiewerkzaamheden uit. Er was 2346 ton dina's, 580 ton chamotte en 86 ton schaars magnesiet nodig.
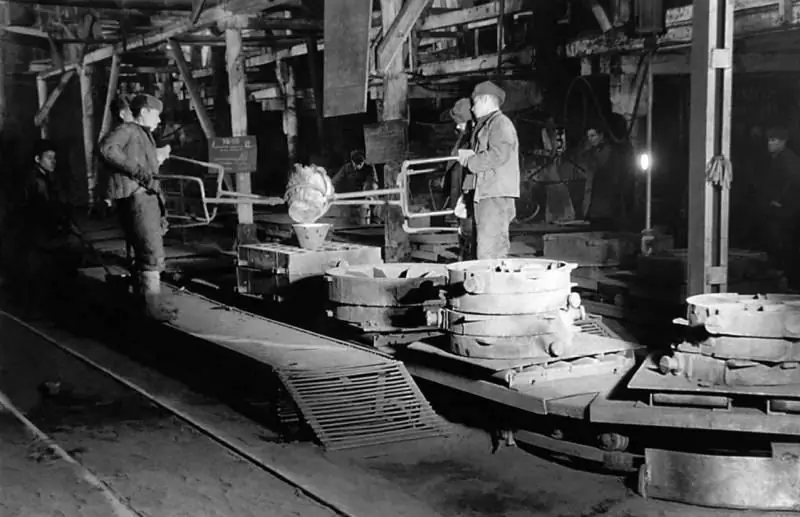
Tegen het midden van 1942, in tankfabriek nr. 183, ontwikkelde de situatie zich op een vergelijkbare manier - de staalproductie bleef achter bij de mechanische assemblage. En we moesten de T-34-rompen "importeren" uit Uralmash.
Een van de redenen was het gebrek aan vuurvaste materialen voor de reparatie van openhaarden, die in het voorjaar van 1942 op hun limiet werkten. Als gevolg hiervan waren in het najaar slechts 2 van de 6 openhaarden in bedrijf en werden de smeltvolumes pas in de tweede helft van 1943 hersteld.
De situatie met vuurvaste elementen in de structuur van het Sovjetdefensiecomplex tijdens de Grote Patriottische Oorlog illustreert duidelijk de complexiteit van de situatie in het achterland van het land.
Een chronisch tekort aan, in het algemeen, niet het meest high-tech product had een directe invloed op het productietempo van gepantserde voertuigen.