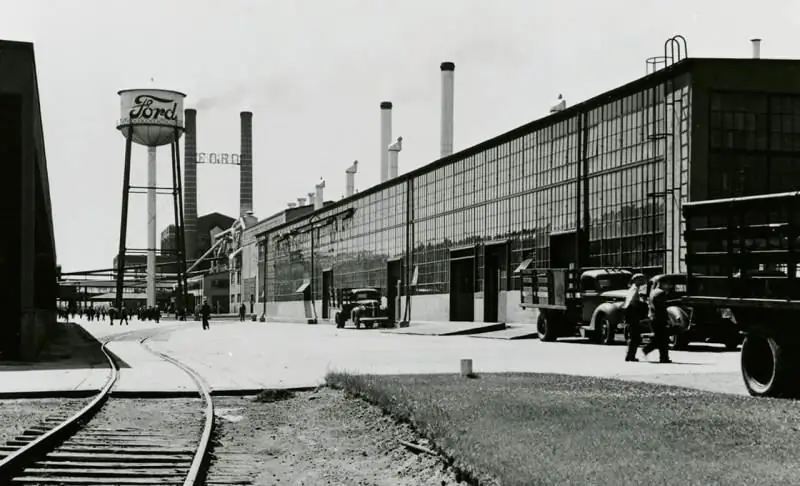
Strategische technologieën
Alvorens kennis te maken met de kenmerken van de gepantserde productie in de Michigan Ford-fabriek in Detroit (VS), is het de moeite waard om kort de omstandigheden uit te leggen waaronder de gepantserde industrie in de USSR tot stand kwam. Zoals je weet, wordt alles geleerd door te vergelijken.
De wapenproductie tijdens de Tweede Wereldoorlog was een van de belangrijkste factoren voor strategisch voordeel. Met het begin van de oorlog bevond de Sovjet-Unie zich in een rampzalige positie - alle gepantserde productie was geconcentreerd in het Europese deel van het land. De snelle opmars van het Duitse leger zou de productie van tankpantser in het land volledig kunnen lamleggen. Alleen ten koste van ongelooflijke inspanningen om aan het begin van de oorlog een deel van de fabrieken naar het oosten te evacueren, was het mogelijk om de productie van bepantsering te herstellen. De belangrijkste "gepantserde fabrieken" waren de metallurgische fabrieken Kuznetsk, Nizhny Tagil en Magnitogorsk.
Maar de zaak bleef niet beperkt tot een simpele verplaatsing van de productie naar een nieuwe locatie achter de frontlinie. De meeste nieuwe fabrieken waren niet aangepast aan het smelten van tankpantser - voor de oorlog werkten de fabrieken voor de behoeften van het Volkscommissariaat voor ferrometallurgie. Oorlogstijd heeft zijn eigen aanpassingen toegevoegd. Nu de open haardovens vaak laaggeschoolde arbeiders hadden, was er een acuut probleem van het ontbreken van speciale thermische, pers- en metaalbewerkingsapparatuur. Daarom ging de overdracht van de wapenproductie gepaard met een serieuze herstructurering van de technologie zelf voor het smelten van militair staal. Het was dus noodzakelijk om de productie aan te passen aan de belangrijkste openhaardovens voor 120-180 ton, exclusief het proces van diffusie-deoxidatie. Het uitharden van pantserplaten en pantseronderdelen moest in water worden uitgevoerd.
Een dergelijke vereenvoudiging kon niet anders dan de kwaliteit van het ontvangen pantser beïnvloeden. Dit geldt met name voor het moeilijkst te vervaardigen tankstaal 8C met een hoge hardheid. De allereerste monsters van pantserplaten tijdens tests vertoonden significante leisteen en gelaagdheid van de breuk, een sterke neiging tot scheurvorming tijdens lassen en rechttrekken. Bovendien onthulden veldtesten de buitensporige kwetsbaarheid van de pantsermonsters tijdens granaatvuur.
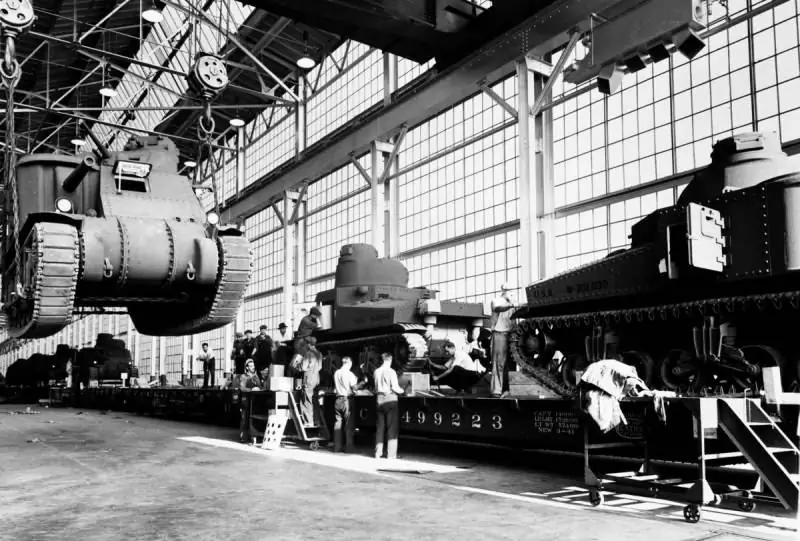
Dergelijke gebreken konden niet worden genegeerd. En in de gespecialiseerde TsNII-48 hebben ze een aantal verbeteringen ontwikkeld. Allereerst zou pantserstaal vanaf nu alleen in voorverwarmde ovens worden gesmolten na het smelten van "civiele" staalsoorten. Het staal moest minstens anderhalf uur koken in het openhaardsmeltbad en in vierkante of bolle vormen gegoten worden. Bovendien hebben metaalbewerkers speciale aandacht besteed aan het zwavelgehalte in het oorspronkelijke ruwijzer (niet meer dan 0,06%), evenals aan koolstof en mangaan. In combinatie met andere maatregelen maakte dit het mogelijk om de kwaliteit van het pantser te verbeteren. In het bijzonder om de leisteen en gelaagdheid van de breuk te verminderen.
Een belangrijk probleem was de technologie van warmtebehandeling van binnenlandse bepantsering. Simpel gezegd kostte het harden en ontlaten van de pantserplaten te veel tijd en energie en ontbrak de benodigde apparatuur. Het proces moest worden vereenvoudigd. In dit verband zullen we een typisch voorbeeld geven. In 1942 slaagden de metallurgen van TsNII-48 erin om het proces van thermische voorbereiding zo veel te vereenvoudigen dat ze alleen voor delen van de bodem van KV- en T-34-tanks ongeveer 3230 ovenuren per 100 rompen bespaarden.
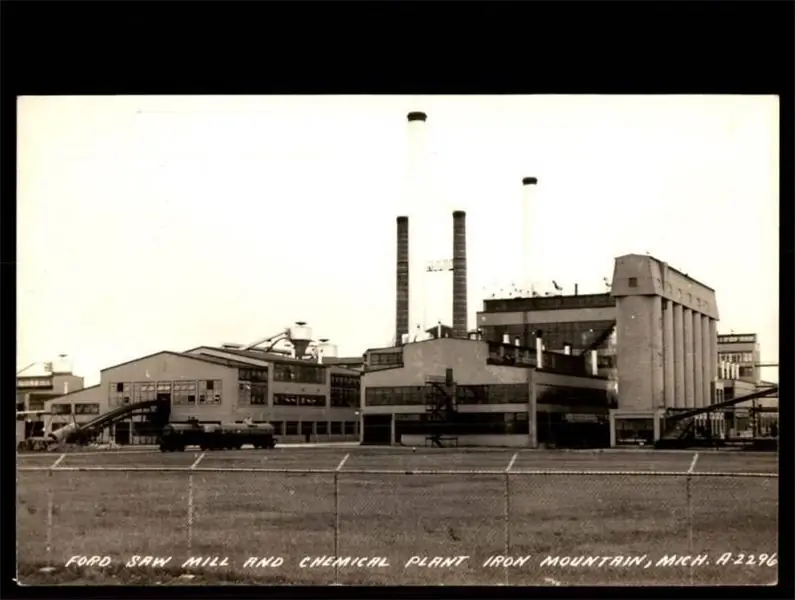
Desalniettemin waren de voorwaarden voor de productie van strategisch belangrijke tankbepantsering tot het einde van de oorlog in de Sovjet-Unie verre van vereist. Hetzelfde kan niet gezegd worden over de militaire industrie van de overzeese partner, wiens grondgebied niet werd aangetast door de wereldoorlog. De Sovjet metallurgische ingenieurs moesten hier op 26 februari 1945, 72 dagen voor de overwinning, nog eens voor zorgen.
Amerikaanse luxe
De weinig bekende geschiedenis van het bezoek van de Sovjetdelegatie aan de Ford-pantserfabriek in Detroit werd aangekondigd door Vasily Vladimirovich Zapariy, kandidaat voor historische wetenschappen van het Instituut voor Geschiedenis en Archeologie van de Oeral-afdeling van de Russische Academie van Wetenschappen. Het materiaal van de wetenschapper is gebaseerd op het rapport van Sovjet-metallurgen over de resultaten van een reis naar de Verenigde Staten, opgeslagen in het Russian State Archive of Economics (RGAE). Opgemerkt moet worden dat de RGAE slechts een schatkamer is van archiefdocumenten uit het tijdperk van de Grote Patriottische Oorlog met betrekking tot de productie van militaire uitrusting en uitrusting. Het blijft alleen om te raden hoeveel geheimen het archief nog meer bewaart in het tot nu toe geclassificeerde bewijsmateriaal.
Volgens ingenieurs die terugkeerden uit Detroit, was de gepantserde werkplaats van de Ford-fabriek een gebouw bestaande uit twee overspanningen van 273 meter lang, 30 meter breed en ongeveer 10 meter hoog. Tegelijkertijd rook de winkel geen pantser. Het was voornamelijk bedoeld voor warmtebehandeling en het snijden van staal. Dit wekte natuurlijk bijzondere belangstelling onder Sovjet-metallurgen, gezien de hierboven beschreven problemen van de binnenlandse gepantserde productie. Het belangrijkste productieprofiel van de Ford Motors-werkplaats was het werken met bepantsering tot 76 mm dik. Warmtebehandelde staalplaten werden gebruikt om de rompen van lichte en middelzware gepantserde voertuigen te lassen in andere fabrieken in Detroit.
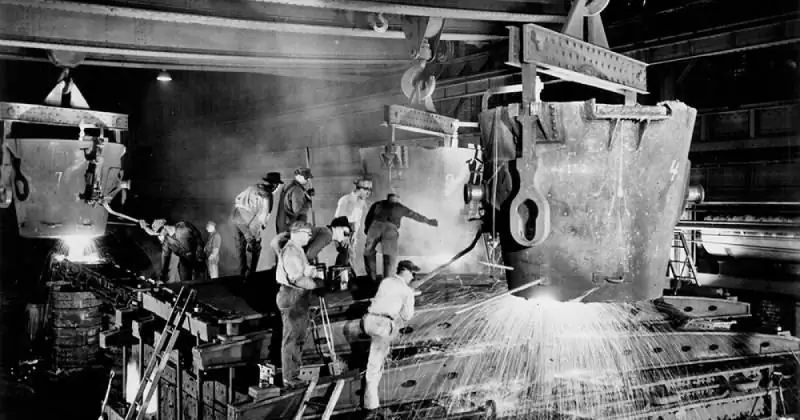
Allereerst maakte de mechanisatie van het productieproces indruk op de Ford-werkplaatsen. Na het smelten en rollen werden de pantserplaten op hydraulische tafelladers United afgeleverd bij de warmtebehandelingswinkel. De laders namen op hun beurt het pantser van de spoorwegplatforms in de buurt van de werkplaats. In de werkplaats zelf waren twee brugkranen ontworpen om pantserplaten te verplaatsen tijdens alle technologische operaties, met uitzondering van verhardingsprocessen.
Om de noodzakelijke kristalstructuur van het pantser te creëren, werd een beroep gedaan op twee persen, elk met een inspanning van 2500 ton, vijf methodische ovens met een transportband van 70 meter en vijf ovens met een gastempereersysteem van 100 meter. Water werd aan de pantserhardingspersen geleverd door zes pompen tegelijk te laten werken, die meer dan 3700 liter per minuut pompten. Zoals Russische ingenieurs schreven, waren de complexiteit en de kosten van het ontwerp van dergelijke persen, die tegelijkertijd roodgloeiend pantser konden stempelen en koelen, onbetaalbaar. Tegelijkertijd waren er twijfels over de wenselijkheid van het gebruik van persen voor bepantsering met een dikte van 30-76 mm. Hier kwam de intensiteit van de watertoevoer voor koeling naar voren.
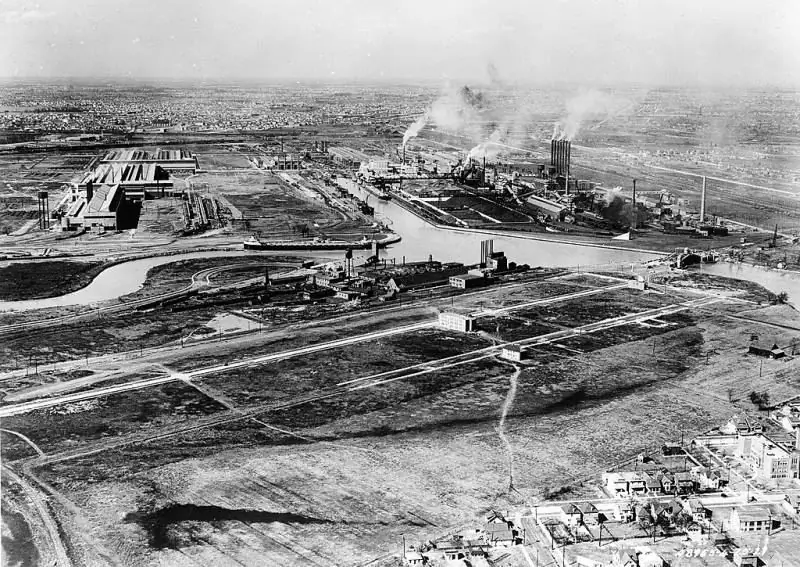
De persen van 2.500 ton waren niet de enigen in het gepantserde voertuig van Ford. Toledo-persen # 206 waren bezig met het snijden van dunne bepantsering en ontwikkelden een druk van 161 ton. Voor pantsers dikker dan 2,5 cm werd uitsluitend vuursnijden toegepast.
Tijdens een bezoek aan de onderneming konden metallurgen het proces van het verharden van dunne kogelvrije bepantsering zien. Het bleef 15 seconden onder een pers van 1000 ton en daarna werd het vel 2,5 uur gestuurd om af te koelen bij 900 graden Celsius en voor vier uur vakantie bij 593 graden.
Al deze technische rijkdom werd waargenomen door Sovjet-ingenieurs, afgezien van verschillende "kleine accessoires": lasmachines, freesmachines, scharen en dergelijke.
Het belangrijkste kenmerk van de warmtebehandeling van het pantser was de continue productiestroom. In bijna alle stadia van de verwerking waren staalplaten in beweging op rollen- en kettingbanen. De transportband werd bestuurd vanaf een centrale console. In een van de laatste fasen werden alle pantserplaten geïnspecteerd op het niveau van Brinell-hardheid. In dit geval moet de fluctuatie van de testparameter van blad tot blad minimaal zijn - niet meer dan 0,2 mm.
Van bijzonder belang voor de Sovjet-delegatie waren twee straalmachines, die de pantserplaten bijna na elke technologische operatie schoonmaakten. Zo'n perfectionisme en zo'n luxe konden alleen Amerikanen zich veroorloven, ver van de ontberingen van oorlogstijd.