Patriottisme van de industriële elite van de Sovjet-Unie werd gecombineerd met een gezamenlijke verantwoordelijkheid voor het eindresultaat
Interindustriële interactie te allen tijde - zowel in het Russische rijk als in de USSR, en vandaag - behoorde niet tot de sterke punten van de binnenlandse industrie. In tegenstelling tot Duitsland of de Verenigde Staten, waar contractuele verplichtingen een onveranderlijke en bijna heilige kracht hadden en hebben.
Neem bijvoorbeeld de relatie tussen Russische metaalbewerkers en machinebouwers. In de tweede helft van de 19e eeuw ontvingen nieuwe transporttechnische fabrieken en scheepswerven niet de vereiste hoeveelheid industriële metalen van de Oeral-mijnwerkers. Die achtte het onrendabel om veel relatief goedkope gewalste producten te maken, aangezien dezelfde winst werd behaald door een veel kleiner volume duur dakijzer. Het ontbrekende metaal voor auto-assen, motorassen en scheepshuid moest in het buitenland worden aangekocht. Pas tegen het einde van de eeuw werd het probleem opgelost door de Zuid-Russische metallurgische fabrieken, opgericht door Belgische of Franse industriëlen. In de Oeral bouwden de Fransen ook één fabriek - Chusovskaya.
Het lijkt erop dat dergelijke grillen in de Sovjettijd uitgesloten waren. Bovendien voorzagen de metallurgische fabrieken die in de jaren '30 werden gebouwd, het land van metaal als geheel. Telkens wanneer machinebouwers nieuwe complexe soorten gewalste producten vroegen, beheersten metaalbewerkers ze echter jarenlang of zelfs decennia.
departementaal feodalisme
Laten we eens kijken naar de geschiedenis van Uralvagonzavod. Al in de eerste projecten was het de bedoeling om massief gewalste stalen wielen onder de vierassige auto's te gebruiken, aangezien de ontwerpcapaciteit zijn ontwerpcapaciteit bereikte, waarvan de leverancier was gepland voor de nabijgelegen Novo-Tagil Metallurgical Plant. Deze laatste werd echter gebouwd door de metallurgische afdeling, en het stelde de bouw van de wielwalserij uit tot 1938-1942, en niet in de eerste plaats. Hierdoor is de zaak niet voor de oorlog begonnen. En na de oorlog was de verhuur van wielen niet zo geïnteresseerd in metaalbewerkers. Resultaat: tot het midden van de jaren 50 verlieten Tagil-auto's de fabriek op gietijzeren wielen met een korte levensduur in plaats van stalen. Dit bracht enorme verliezen voor de spoorwegarbeiders met zich mee, maar er was geen keuze: of zulke auto's, of geen.
Hetzelfde gebeurde met de introductie van laaggelegeerde staalsoorten in de koetsbouw. Ze beloofden een merkbare vermindering van het eigen gewicht van het rollend materieel met behoud van alle prestatiekenmerken. De ontwerpers van Uralvagonzavod begonnen eind jaren '30 met het ontwerpen van auto's gemaakt van laaggelegeerd metaal, maar hun serieproductie begon pas in de tweede helft van de jaren '50, omdat metaalbewerkers geen geschikte gewalste producten of ferrolegeringen voor het gieten van onderdelen leverden.
Het moet gezegd worden dat het virus van het departementale feodalisme de machinebouwers zelf trof. In de zomer van 1937 vond een interessant verhaal plaats dat de interagency-relaties van die tijd kenmerkte. Het Hoofddirectoraat van Metallurgische Ondernemingen stuurde naar Uralvagonzavod een order voor vijfduizend ton blanks voor de onlangs gelanceerde verbandmolen van de Novo-Tagil-fabriek. Het hoofddirectoraat van Transport Engineering was verontwaardigd over de aantasting van een ondergeschikte onderneming. Plaatsvervangend hoofd van de Hoofddirectie G. G. Op 11 juli stuurde Aleksandrov een brief aan GUMP en Uralvagonzavod met de volgende verklaring: "We zijn buitengewoon verrast dat de oplossing van een zo belangrijk probleem als het organiseren van de productie van een blanco verband in Uralvagonzavod werd uitgevoerd zonder onze deelname, en nog meer - we kregen niet eens een kopie van de outfit die naar Uralvagonzavod was gestuurd … Ik vraag u om een vaste procedure vast te stellen voor het verstrekken van blanco's aan onze fabrieken, alleen in overleg met ons en via Glavtransmash."
Dientengevolge werd metaalbewerkers het verbandstaal geweigerd, naar verluidt vanwege de technische onmogelijkheid om ingots van hoge kwaliteit in de open haard van de Uralvagonzavod te gieten. Ondertussen, al in 1936, werd hier een axiale plano gegoten, en in 1937 - ingots voor het rollen van platen. Daarom moesten de blokken voor de lijkwadefabriek, die zich op enkele kilometers van UVZ bevindt, van de fabrieken in Vyksa en Kuznetsk worden vervoerd. Bovendien liet de kwaliteit te wensen over en waren de aanvoervolumes onvoldoende.
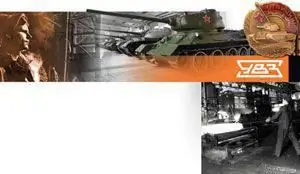
In 1938 herhaalde de geschiedenis zich. De belangrijkste verbruiker van UVZ-staven was de Molotov (dat wil zeggen Perm) Artillery Plant, die aan het einde van het jaar een partij blanco's ontving. En slechts een klein aantal van hen ging naar de verbandwinkel, die het ontbrekende metaal opnieuw voor twee of twee en een half duizend kilometer moest importeren. De belangen van de industrie in de distributie van Uralvagonzavodsk-staal hadden duidelijk de overhand.
Ook de afdelingsziekte spaarde de defensie-industrie niet. Talloze publicaties over de geschiedenis van de Sovjettankbouw staan vol met voorbeelden van hoe de bouw van prototypes of de inzet van massaproductie werd vertraagd door het niet leveren van metaal, met name bepantsering.
En zelfs vandaag is het sectorale eigenbelang nergens heen gegaan, het is alleen van vorm veranderd. Verzoeken om nieuw gevormde vormen van gewalste producten worden eenvoudig bestreden met exorbitante prijzen. Over een gecoördineerd beleid hoeft niet te worden gesproken. Na de ineenstorting van de wisselkoers van de roebel aan het begin van 2014-2015, verhoogden metallurgische bedrijven de prijzen voor rollend materieel met 30-60 procent. En ze begonnen meteen te klagen over de machinebouwers voor de apparatuur die in prijs was gestegen - de machines worden tenslotte in Rusland geproduceerd en zijn niet gebonden aan de dollarkoers.
Het lijkt erop dat er in ons land maar één remedie is voor sectoroverschrijdende problemen: het creëren van verticaal geïntegreerde systemen, waarbij het erts dat door onze eigen krachten wordt gewonnen eerst in metaal wordt omgezet en vervolgens in afgewerkte machines.
eenheid in oorlogstijd
Er is echter een korte periode in onze geschiedenis waarin de belangen van de industrie op de achtergrond zijn geraakt. We hebben het over de Grote Vaderlandse Oorlog. Het onbetwistbare patriottisme van de Sovjet-industriële elite in die tijd ging gepaard met de gezamenlijke verantwoordelijkheid van alle betrokkenen bij de defensieproductie voor het eindresultaat. Dat wil zeggen, de directeur van de gepantserde walserij was niet zozeer verantwoordelijk voor het volume gesmolten en gewalst staal, maar voor het aantal gebouwde tanks.
De belangrijkste stap in deze richting werd gemaakt door de directeur van NII-48 A. S. Zavyalov. In de begindagen van de oorlog wendde hij zich tot de regering met een voorstel om het instituut te instrueren technologieën te introduceren voor de productie van speciaal staal en gepantserde constructies bij bedrijven in het oosten van het land, die zich voor het eerst bezighielden met de productie van gepantserde voertuigen. Begin juli leidden teams van specialisten van NII-48 de technologische herstructurering van 14 grootste ondernemingen. Onder hen waren de Magnitogorsk en Kuznetsk Metallurgische Fabrieken, de Novo-Tagil en Chusovka Metallurgische Fabrieken, de Oeral Heavy Machine Building Plant, de Gorky Krasnoye Sormovo, de Stalingrad Tractor Plant, de Stalingrad Red October en No. 264. Zo schond Zavyalov de vooroorlogs taboe: op de lijst stonden ondernemingen van drie volkscommissariaten.
Patriottisme en gedwongen onderdrukking van departementaal egoïsme zorgden voor een ongekende ontwikkeling van defensieproducten in de Sovjetmetallurgie, noch in de vooroorlogse, noch in de naoorlogse periode. Binnen enkele maanden werd in het oosten van het land (voornamelijk in de Oeral) de productie van ferromangaan, ferrosilicium, ferrochroom, ferrovanadium en andere legeringen georganiseerd, zonder welke het onmogelijk is om pantserstaal te verkrijgen. Na het verlies van de westelijke regio's bleef Chelyabinsk de enige fabriek van ijzerlegeringen in de USSR. Daarop werd in korte tijd het smelten met twee en een half keer verhoogd. Er werden 25 soorten producten geproduceerd, maar de meeste waren van verschillende soorten ferrochroom. Het smelten van ferromangaan vond plaats in hoogovens, en niet alleen in oude hoogovens met een laag tonnage van de fabrieken in Nizhniy Tagil en Kushvinsky, maar ook in een grote moderne oven van de Magnitogorsk Combine. In tegenstelling tot alle vooroorlogse ideeën, werd ferrochroom in de tweede helft van 1941 in hun hoogovens gesmolten door metallurgen van de Nizhniy Tagil- en Serov-fabrieken, en wetenschappers van de Oeral-afdeling van de USSR Academy of Sciences leverden grote hulp bij het creëren van een nieuwe technologie. Later werd het smelten van ferrosilicium onder de knie in de hoogovens van Serov.
Er waren voor de oorlog geen gepantserde kampen in de Oeral of in West-Siberië, ze moesten haastig worden overgebracht van ondernemingen die zich in het gevechtsgebied bevonden.
In de zomer van 1941 was het geëvacueerde materieel nog onderweg. En toen stelde de hoofdmonteur van de Magnitogorsk Combine N. A. Ryzhenko voor om het pantser op een bloeiende molen te rollen. Ondanks het grote risico werd het idee uitgevoerd. En in oktober trad een gepantserd kamp, dat uit de fabriek van Mariupol was gehaald, in dienst. Het werd in slechts 54 dagen geassembleerd. Volgens de vooroorlogse maatstaven duurde dit een jaar.
De fabriek van Novo-Tagil kreeg het kamp uit Leningrad. De voorbereidingen voor de opname begonnen in juli, aanvankelijk werd aangenomen dat het op de plaats van het verband zou worden gemonteerd. Het verbandkamp werd gedemonteerd, maar het bleek dat de oude voorraad niet voldoende was om het pantserkamp te installeren en elders moest worden geplaatst. De oorlog dwong te doen wat tot voor kort als onmogelijk werd beschouwd: slechts een jaar geleden hadden pogingen om industriële constructie uit te voeren door een geïntegreerde "hogesnelheids" -methode in Nizhny Tagil op zijn best een gedeeltelijk succes, en in de zomer van 1941 de meest complexe bouwoperatie was bijna perfect. Op 10 september werd de eerste Tagil-staalplaat een maand eerder dan gepland gewalst. In totaal werd tegen het einde van het jaar 13.650 ton plaatwerk verkregen, waaronder ongeveer 60 procent bepantsering (de molen werd getest op koolstofstaal en in oktober - december werd koolstofstaal gewalst met een tekort aan pantserstaven). Als gevolg hiervan overschreed de maandelijkse productie van pantserplaten in de Oeral-fabrieken al in januari 1942 in de hele vooroorlogse Sovjet-Unie meer dan zes maanden.
Niet minder verrassende gebeurtenissen vonden plaats bij andere onbekende bedrijven. Tijdens de oorlog was de Zlatoust Metallurgical Plant inferieur aan de Magnitogorsk Combine in termen van het volume van het smelten en gewalst staal, maar het overtrof het aanzienlijk in zijn productmix - hier werden ongeveer 300 soorten gelegeerd en koolstofstaal geproduceerd. Zonder bevoorrading van Zlatoust zou de productie van vele soorten wapens, voornamelijk tankmotoren, zijn gestopt.
Oude fabrieken in de Oeral bleken onmisbaar bij de productie van kleine series bijzonder hoogwaardig staal. Zo werd metaal van Serov Metallurgical, de belangrijkste fabrikant van gekalibreerde gewalste producten, in elke Sovjettank geïnvesteerd. De fabriek in Nizhnesalda schakelde over op het smelten van nikkelijzer en staal. Deze lijst kan eindeloos worden voortgezet - tijdens de oorlogsjaren werd overal waar minstens één koepel was, metaal van wapenkwaliteit gesmolten.
Er is een merkwaardig verhaal met fluxen voor automatisch lassen. Voor en aan het begin van de oorlog werden ze gesmolten in een van de ondernemingen van Donbass, na de bezetting waarvan de gecentraliseerde bevoorrading volledig stopte. Eind 1941 begonnen medewerkers van het Instituut voor Elektrisch Welding van de Academie van Wetenschappen van de Oekraïense SSR te zoeken naar vervangende materialen die in min of meer bruikbare staat in de Oeral beschikbaar waren. En ze vonden ze - in de vorm van hoogovenslakken van de metallurgische fabriek Ashinskiy. Er waren slechts kleine verbeteringen nodig: de hoogovens verrijkten hun slakken met mangaan en maakten er zo een volledig geschikt vloeimiddel van. De apparatuur die nodig was voor het testen werd rechtstreeks van Nizhny Tagil naar Asha gebracht.
Voorbeelden van lokale samenwerking tussen tank- en metallurgische fabrieken zijn zeer indicatief. Vóór de lancering van zijn eigen faciliteiten, werd warmtebehandeling van tankonderdelen van de Ural Tank Plant nr. 183 uitgevoerd in de Nizhniy Tagil Metallurgical Plant.
Het succesvolle werk van UTZ-gieterijarbeiders werd enorm vergemakkelijkt door de hulp van de naburige vuurvaste kleifabriek Nizhniy Tagil, die de productie van vuurvaste vuursteenpluggen van hoge kwaliteit op gang bracht. Dit maakte het mogelijk om probleemloos gieten van zwaar pantserstaal voor vormgieten uit te voeren.
In 1942-1945 werkten open-haardovens bij UTZ voornamelijk op cokesoven en hoogovengas van de Novo-Tagil Metallurgical en Nizhniy Tagil Coke Plants. De gasleiding is sinds februari 1942 in gebruik. De eigen gascentrale van fabriek nr. 183 voorzag in niet meer dan 40 procent van de behoeften.
Soms was een simpel advies voldoende om een probleem op te lossen. De informatie van lokale metallurgen over een kleine mangaanmijn die in de jaren 1870 werd ontwikkeld, hielp om enkele weken voor de start van de leveringen van ferromangaan te overleven zonder het gieten van tanksporen te stoppen.
Nog een voorbeeld: naarmate de productie van pantserstaal toenam, kon de openhaardwinkel het smelten van metaal voor de koppen van luchtbommen niet meer bijbenen. Het was niet mogelijk om het van buitenaf te krijgen. Directeur Yu. E. Maksarev herinnerde zich het verloop van verdere gebeurtenissen in zijn memoires: Toen ik op een van de vergaderingen in het stadscomité was, ontmoette ik de directeur van de oude, nog steeds Demidov-fabriek en vroeg me de casting van de bomkoppen. Hij zei: ik kan niet helpen met staal, maar met advies zal ik helpen. En toen ik bij zijn fabriek kwam, liet hij me een Bessemer-converter van anderhalve ton zien met medium blazen. Hij gaf me de tekeningen en zei dat hij weet dat we een goede gemechaniseerde ijzergieterij hebben, en uw converters zullen lassen”. Zo verscheen de bestelling voor de fabriek van 8 september 1942 op de organisatie in de Griffin-wielwinkel van de Bessemer-sectie van drie kleine converters (elk anderhalve ton metaal). Op 25 september werd het project voorbereid door de ontwerp- en technologische afdeling van het kapitaalconstructiebeheer, de specialisten van de hoofdmonteurafdeling lasten snel converters en ketels - opslagtanks voor vloeibaar ijzer. Het proefdraaien van de afdeling Bessemer en het gieten van een experimentele batch van vijf namen van onderdelen vond plaats rond oktober-november 1942. De serieproductie begon eind november.
Aan het einde van het onderwerp: de samenwerking van metaalbewerkers en tankbouwers in oorlogstijd werkte in beide richtingen. De installateurs van de Ural Tank Plant hebben deelgenomen aan de ingebruikname van veel nieuwe eenheden van de Novo-Tagil Metallurgical Plant. In mei 1944 werd een aanzienlijk aantal voeringplaten voor de reparatie van de hoogoven vervaardigd in de gepantserde torengieterij.
Maar de belangrijkste assistent van de metaalbewerkers was natuurlijk de Ural Heavy Machine Building Plant. De orderboeken voor UZTM voor 1942-1945 staan letterlijk vol met documenten over de productie van reserveonderdelen en apparaten voor metallurgische doeleinden - zowel voor de behoeften van de tankindustrie als voor de ondernemingen van het Volkscommissariaat voor ferrometallurgie. In de herfst van 1942 werd een speciale afdeling voor de productie van apparatuur voor metallurgische fabrieken officieel hersteld in het UZTM. Het kreeg de code "Divisie 15" en was ondergeschikt aan de adjunct-directeur voor inkoopwinkels en cascoproductie.
Succes op het snijvlak van industrieën
De samenwerking van metaalbewerkers en tankbouwers heeft geleid tot het ontstaan van een aantal technologieën die zonder overdrijving echte wetenschappelijke en technische doorbraken kunnen worden genoemd.
Nadat ze pantserstaal tot platen hadden gesmolten en gewalst, brachten metaalbewerkers hun producten over naar de productie van gepantserde rompen. Hier werd het metaal volgens het sjabloon in de overeenkomstige delen gesneden. Bij de productie van "vierendertig" werd vooral veel moeite geleverd door twee delen van de romp: fenders (de schuine zijde van de zijkant) en de verticale zijplaat. Beiden waren lang, zelfs in brede stroken met schuine sneden langs de randen.
Het idee kwam natuurlijk op om een meetstrook te rollen die even breed was als de afgewerkte delen. Het werd voor het eerst geformuleerd door de gepantserde auto's van de Mariupol-fabriek in de zomer van 1941. Voor het proefwalsen kozen we een slabbenfabriek in Zaporizhstal, waar twee echelons pantserstaven werden gestuurd. Maar toen hadden ze geen tijd om aan de slag te gaan: de oprukkende Duitse troepen veroverden zowel de echelons als Zaporozhye zelf.
Aan het begin van 1941-1942, tijdens de evacuatie en de ontwikkeling van de productie van bepantsering in de nieuwe fabrieken, was er niet genoeg streep. In mei 1942 ontving het Volkscommissariaat van de ferrometallurgie echter opnieuw het bevel om het te huren voor T-34- en KV-tanks. De taak bleek moeilijk: de toleranties in de breedte mogen niet groter zijn dan -2 / + 5 millimeter, de halvemaanvorm (bocht) voor de totale lengte van het onderdeel was 5 millimeter. Scheuren, zonsondergangen en delaminatie aan de randen waren niet toegestaan, zodat het lassen kon worden uitgevoerd zonder machinale bewerking of vlamsnijden.
Experimenteel werk begon gelijktijdig in de walserijen van de Magnitogorsk en Kuznetsk metallurgische fabrieken, aanvankelijk zonder enige bijzondere prestaties. De verhuur van onderdelen voor de KV-tanks werd al snel stopgezet, maar de T-34 was eindelijk succesvol. Het team van auteurs, bestaande uit het hoofd van de metallurgische afdeling van de NII-48 G. A. Vinogradov, de hoofdingenieur van de KMK L. E. Vaisberg en de ingenieur van dezelfde fabriek S. E. staat "900" van de spoor- en constructiemolen is een volledig nieuwe methode om "op de rand" te rollen. In januari 1943 werden 280 strips uitgegeven, in februari - 486, in maart - 1636 stuks. In april begon, na alle vereiste tests, de ontwikkeling van de brutoproductie van meetstrips voor de wielkastbekledingen van T-34-tanks. Aanvankelijk werden ze geleverd aan UZTM en de Ural Tank Plant, en vervolgens aan andere fabrieken - fabrikanten van T-34-tanks. Het schroot, dat oorspronkelijk 9,2 procent bedroeg, was in oktober 1943 gedaald tot 2,5 procent en de ondermaatse strips werden gebruikt om kleinere onderdelen te maken.
Een volledige en nauwkeurige beoordeling van de nieuwe technologie wordt gegeven door het overeenkomstige rapport van TsNII-48 van 25 december 1943: "Een fundamenteel nieuwe methode voor het rollen van een brede gepantserde strip" op de rand "werd ontwikkeld, getest en geïntroduceerd in de brutoproductie, die tot voor kort in de USSR en in het buitenland als onhaalbaar werd beschouwd. Het verkrijgen van een gekalibreerde (gemeten) strip met een breedte van het voltooide deel van de gepantserde romp van de T-34-tank maakte het voor de NKTP-fabrieken mogelijk om een nieuwe hoogwaardige technologie toe te passen voor de vervaardiging van gepantserde onderdelen zonder langsranden te snijden. Dankzij de toepassing van de nieuwe methode op een van de belangrijkste gepantserde delen van de T-34 tank (fenders), werd een zeer aanzienlijke tijdwinst (ongeveer 36%) behaald bij het uitsnijden ervan. Besparingen behaald van 8C pantserstaal tot 15 procent en zuurstofbesparing van 15.000 cbm per 1000 rompen”.
Tegen het einde van 1943 werd het rollen van een meetstrip onder de knie voor een ander deel van de T-34-romp - het verticale deel van de zijkant. Het blijft alleen om toe te voegen dat de auteurs van deze uitvinding de Stalin-prijs voor 1943 hebben gekregen.
In dezelfde 1943, door gezamenlijke inspanningen van het laboratorium van het Oekraïense Instituut voor Metalen (onder leiding van PA Aleksandrov) en werknemers van de Kuznetsk Metallurgical Combine en de Ural Tank Plant, werd een speciaal periodiek gewalst profiel ontwikkeld en beheerst in productie voor de aanschaf van massa en kritieke delen van de "vierendertig" - balanceerassen. De eerste experimentele batch van een periodiek profiel werd in december ontvangen bij KMK, begin 1944 begon de serieproductie. In oktober schakelde de Ural Tank Plant volledig over op de productie van balansassen van een nieuwe blank, aan het einde van het jaar sloot UZTM zich daarbij aan. Hierdoor steeg de productiviteit van de smeedhamers met 63 procent en nam het aantal onderdeelbreuken af.
Het succesvolle werk van de tankbouwers werd enorm vergemakkelijkt door het rollend materieel van de verbandmolen van de Novo-Tagil Metallurgical Plant. Vanaf het voorjaar van 1942 leverden ze opgerolde schouderbanden met verminderde bewerkingstoeslagen, in 1943 werden de toeslagen weer verlaagd. In combinatie met het nieuwe snijgereedschap maakte dit het mogelijk om het tijdrovende strippen van schouderbanden strikt volgens schema en zonder veel stress uit te voeren. Een zeldzaam geval: de Volkscommissaris van de Tankindustrie V. A. Malyshev achtte het in zijn bevel van 28 september 1943 nodig om speciale dank uit te spreken aan de Tagil-metallurgen.
En tot slot, het laatste voorbeeld: in 1943 begonnen de velgen van de T-34-ondersteuningstanks, eerst in de fabriek in Chelyabinsk Kirov en vervolgens bij andere ondernemingen, te worden gemaakt van speciaal geprofileerde gewalste producten. Dit succes werd ook opgemerkt in de volgorde van V. A. Malyshev.
Er moet nog aan worden toegevoegd dat de specialisten van het Amerikaanse bedrijf "Chrysler", die de in Korea gevangen T-34-85-tank hebben bestudeerd, vooral de perfectie opmerkten van de stalen blanks waaruit het gevechtsvoertuig was gemaakt. En ook het feit dat ze vaak in de minderheid waren dan de producten van de Amerikaanse metallurgische ondernemingen.