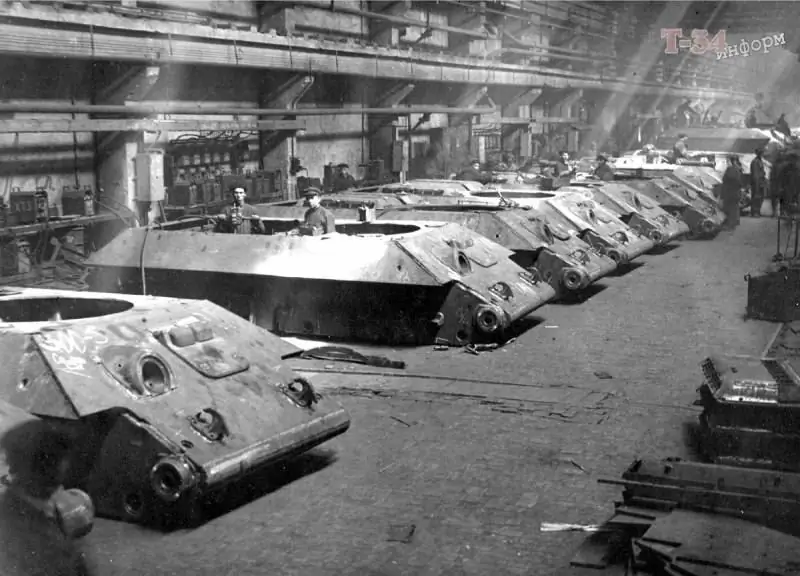
Zwakke schakels van de stalen afscherming
Hoe kan een lawine-achtige toename van de productie van tanks die het front hard nodig heeft? Nikita Melnikov's boek "Tank Industry of the USSR during the Great Patriotic War" geeft gegevens over de achteruitgang van de voorwaarden voor het ontvangen van afgewerkte producten door militaire vertegenwoordigers.
Sinds 15 januari 1942 zijn tankfabrieken zeer "liberaal" in het beoordelen van de kwaliteit van de productie van gepantserde voertuigen. Slechts elke tiende medium tank T-34 en zware KV naar keuze van de militaire vertegenwoordiger werd onderworpen aan een korte run van vijf kilometer. In het geval van de T-60 tanks waren er natuurlijk meer twijfels, dus elke vijfde lichte tank werd onderworpen aan een run. Of misschien waren dergelijke machines aan het front minder nodig, daarom waren ze er zelfs in het stadium van acceptatie strenger tegenover. Dit bevestigt indirect het controleschot van het kanon van elke T-60 die de poorten van de fabrieken verlaat, terwijl de T-34- en KV-kanonnen slechts op elk tiende voertuig werden getest. Het was toegestaan om tanks naar de troepen te sturen met ontbrekende snelheidsmeters, torentje draaiende motoren, intercoms als ze werden vervangen door signaallampen, evenals torenventilatoren. Het laatste punt was gelukkig alleen in de winter toegestaan.
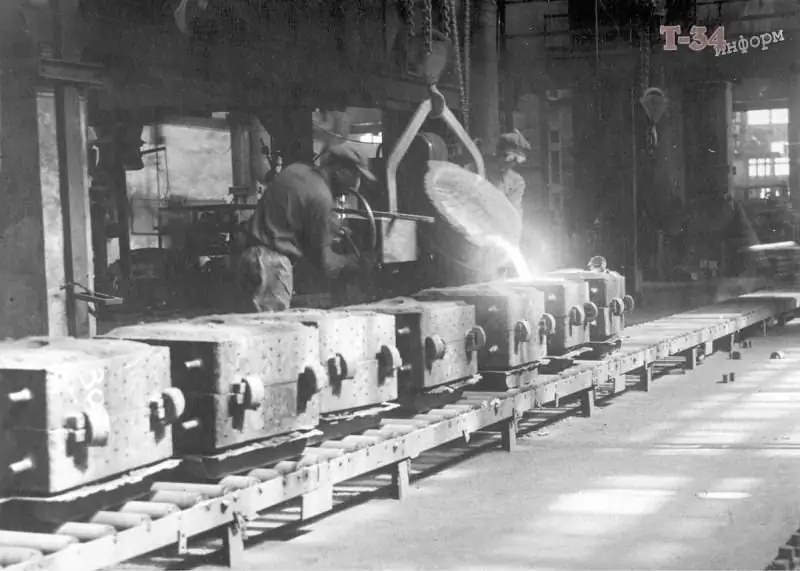
Afzonderlijk moet worden opgemerkt dat de tankindustrie medio 1942 al met succes was omgegaan met de kwantitatieve indicatoren van de productie van gepantserde voertuigen. Uralmash overschreed regelmatig zelfs de productienormen voor tanks, en de Kirov-fabriek in Chelyabinsk verviervoudigde van januari tot maart de productie van de V-2-dieselmotor.
Dergelijke productiegroeipercentages waren grotendeels te wijten aan een ernstige achteruitgang in de kwaliteit van tanks die van de lopende band kwamen. Een illustratief voorbeeld is de 121e Tankbrigade, die tijdens een worp van 250 kilometer de helft van zijn zware KV's verloor door pannes. Het gebeurde in februari 1942. Lange tijd daarna veranderde de situatie niet fundamenteel. In het najaar van 1942 werden 84 KV-tanks geïnspecteerd, die om technische redenen buiten gebruik waren, waardoor niet eens 15 motoruren werden behaald. Meestal waren er defecte motoren, kapotte versnellingsbakken, defecte rollen, onbruikbare triplexen en veel kleine gebreken. In de zomer van 1942 ging tot 35% van alle T-34-tanks verloren, niet omdat ze werden geraakt door vijandelijke granaten of werden opgeblazen door een mijn, maar door het falen van componenten en assemblages (voornamelijk motoren). Nikita Melnikov suggereert in zijn werk dat een deel van de verliezen kan worden toegeschreven aan het lage niveau van bemanningskwalificaties, maar zelfs hiermee rekening houdend, is het percentage niet-gevechtsverliezen te hoog. Dergelijke storingen van de KV en T-34 zouden echter in het veld kunnen worden verholpen, soms door simpelweg de unit of montage te vervangen. Maar het was nutteloos om te vechten met de onbevredigende kwaliteit van het pantser op de T-34 aan de voorkant - de gepantserde rompen waren gekookt van staal met een lage viscositeit, dat, wanneer het werd geraakt door vijandelijke granaten, barsten, delaminatie en spatten veroorzaakte. Vaak vormden zich scheuren op nieuwe machines, wat de kansen van de bemanning op een gunstig resultaat sterk verminderde wanneer een Duitse granaat een scheur of een aangrenzend pantsergebied raakte.
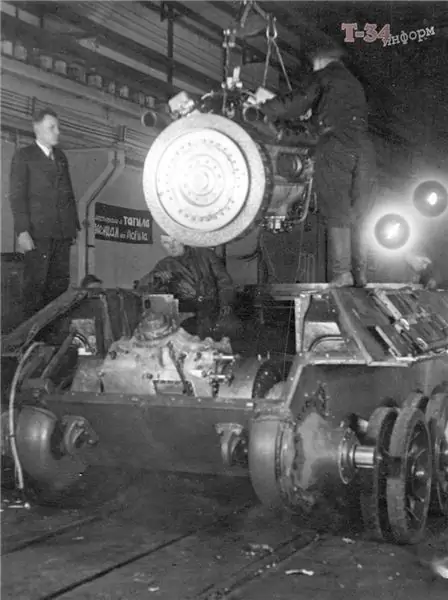
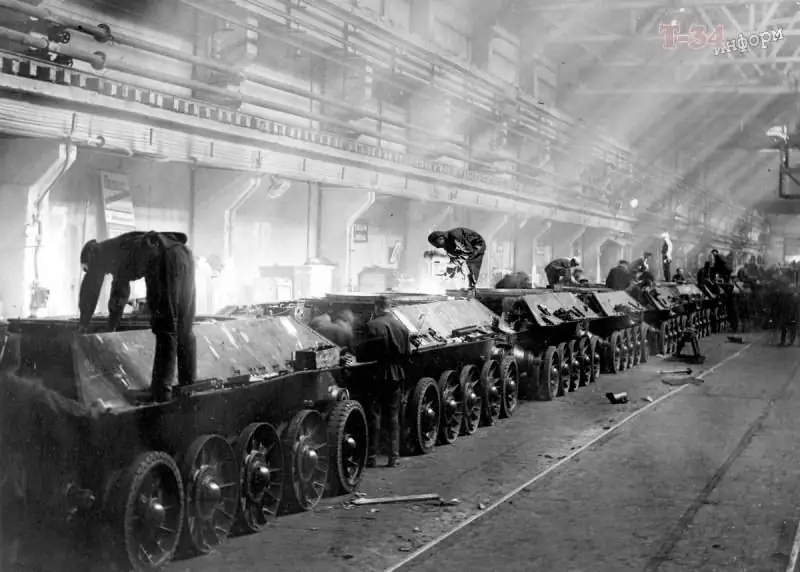
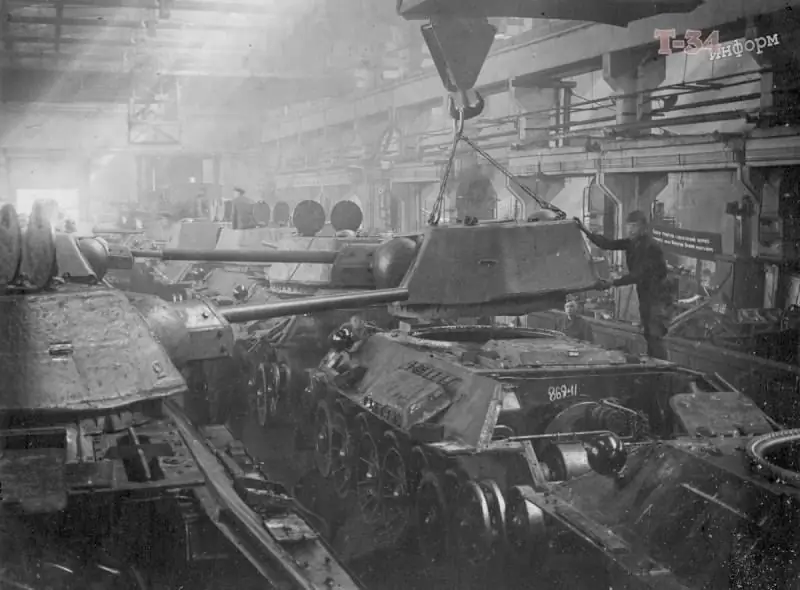
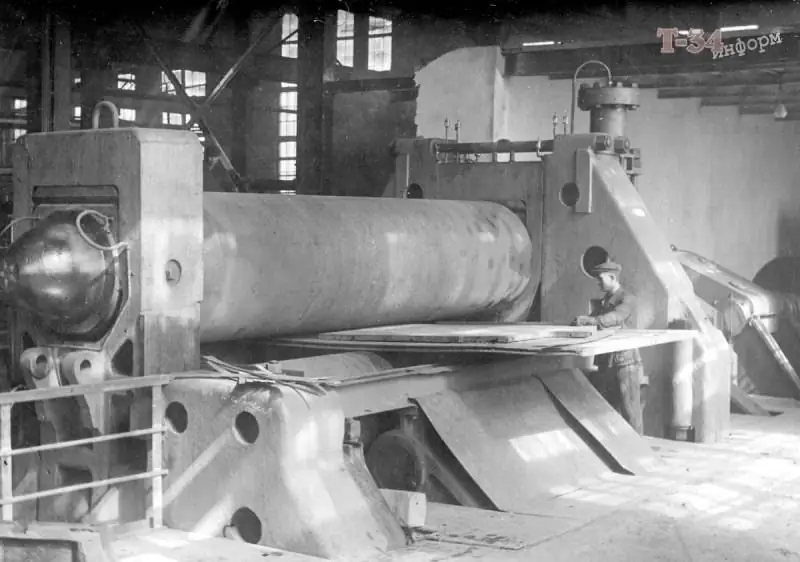
De eerste alarmerende telefoontjes over de komst van T-34-eenheden met scheuren klonken in mei 1942: fabriek # 183 ontving die maand claims voor 13 voertuigen, voor 38 tanks in juni en voor tweeënzeventig T-34's in de eerste tien dagen van juli. … De regering kon in dit geval niet zwijgen en op 5 juni nam het Staatsverdedigingscomité een resolutie aan "Over het verbeteren van de T-34-tanks". Tegelijkertijd kreeg het parket van de USSR de opdracht om de redenen voor deze achteruitgang van de kwaliteit van tanks te onderzoeken.
In de loop van het werk ontdekten de onderzoekers met name tal van feiten over diefstal van producten uit het dieet van werknemers van de tankindustriebedrijven. De fabrieksarbeiders waren gewoon ondervoed. Een voorbeeld van zo'n roofzuchtige houding wordt gegeven in een reeks materialen over Isaac Zaltsman, de meest controversiële leider van tankfabrieken.
Onder de ondernemingen die "zich onderscheidden" in de productie van defecte T-34's, nam de beroemde fabriek in Nizhny Tagil de eerste plaats in. Bovendien viel de piek in het uitbrengen van defecte producten juist op het moment van de leiding van de eerder genoemde Zaltsman. De directeur van de onderneming werd echter, zoals we ons herinneren, niet gedegradeerd, maar onmiddellijk benoemd tot Volkscommissaris van de tankindustrie. Het is duidelijk dat de autoriteiten besloten de hoogste regionen van Vyacheslav Aleksandrovich Malyshev, de 1e Volkscommissaris van de tankindustrie van de USSR, de schuld te geven. Toegegeven, de ontnuchtering kwam een jaar later, in de zomer van 1943, Malyshev werd opnieuw op de plaats van de volkscommissaris gezet, die hij tot het einde van de oorlog behield.
Het parket van de openbare aanklager, die aan het werk was bij de geëvacueerde ondernemingen van de tankindustrie, onthulde naast het half uitgehongerde bestaan van de fabrieksarbeiders nog een ander probleem van de onbevredigende kwaliteit van tanks - een ernstige schending van de productiecyclus.
Vereenvoudiging ten koste van kwaliteit
Zoals je weet, kon de Mariupol-fabriek genoemd naar Iljitsj niet worden verdedigd, het kwam in handen van de vijand en met een massa technologische apparatuur die ze niet konden evacueren. Het was deze onderneming (de enige in het land) die in staat was om volwaardige gepantserde rompen voor de T-34 te produceren die aan alle normen voldoen. In de Oeral kon geen enkele fabriek zoiets bieden, dus begon het onderzoeksteam van het Armored Institute (TsNII-48) de Mariupol-praktijken aan te passen aan de realiteit van de geëvacueerde fabrieken. Voor de productie van hoogwaardige bepantsering in de door GKO vereiste volumes, was er een nijpend tekort aan thermische ovens, dus ontwikkelde het instituut een nieuwe cyclus van verharding van pantseronderdelen. In Mariupol ging de pantserplaat eerst naar verharding, toen naar hoge vakantie, dan weer naar verharding. Ten slotte volgde een lage vakantie. Om de productie te versnellen, werd de eerste verharding aanvankelijk geannuleerd en vervolgens op hoge temperatuur getemperd, wat de taaiheid van het pantserstaal direct beïnvloedt en de kans op scheuren verkleint. Een van de noodzakelijke maatregelen was volgens de specialisten van het Armor Institute om niet één, maar onmiddellijk vier of vijf rijen pantserplaten in de thermische oven te laden. Dit bleek natuurlijk veel sneller te gaan, maar de uiteindelijke kwaliteit van de matten was zeer heterogeen. Interessant is dat het Armored Institute later besloot om de lage tempering-procedure te annuleren, die de restspanningen van het metaal vermindert, wat wederom een negatief effect had op de scheurvorming.
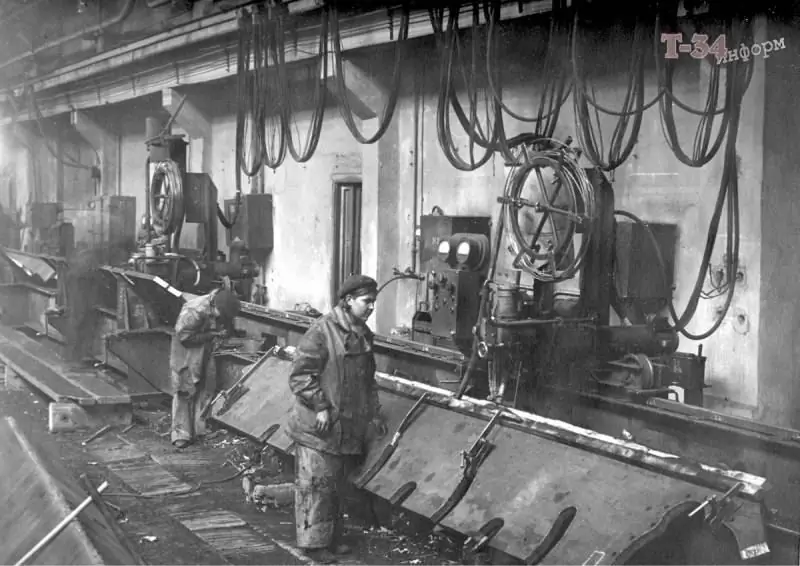
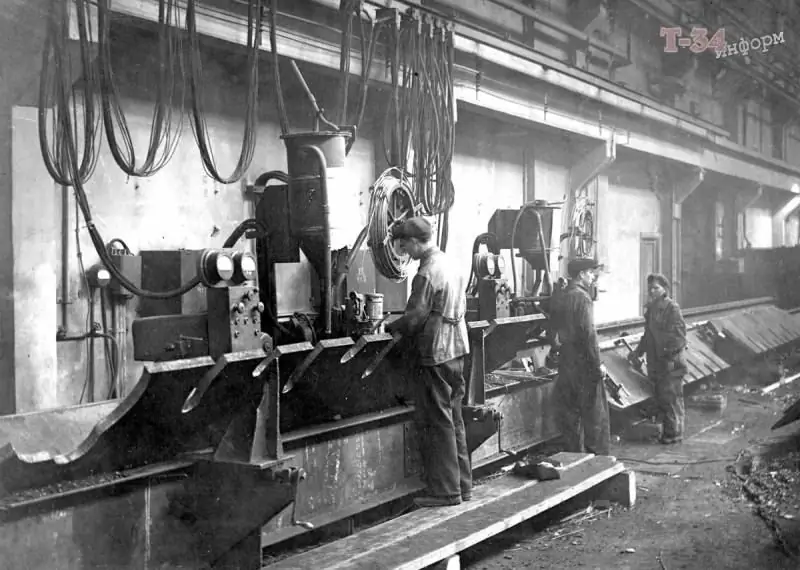
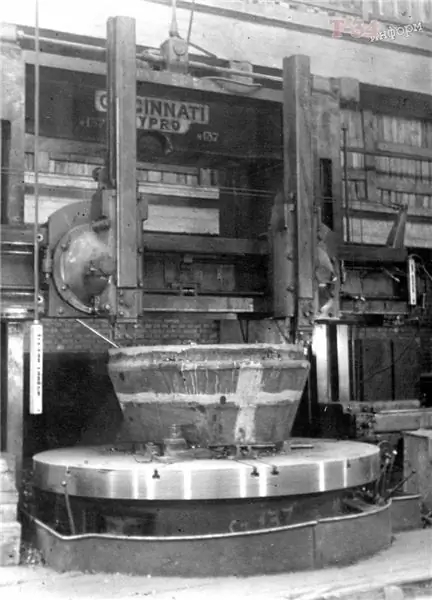
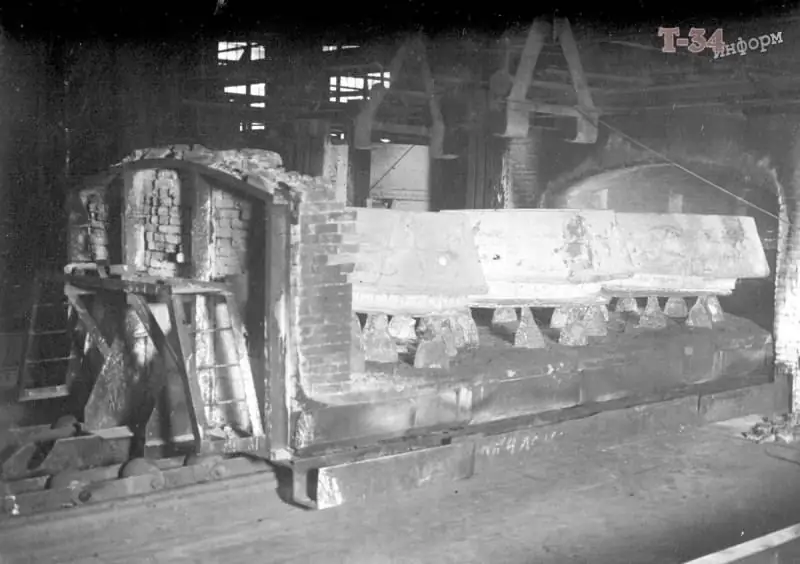
Je kunt gehard staal niet snijden met gassnijders - deze stelling is bij iedereen bekend, maar de realiteit van de productie van T-34 gepantserde rompen wordt gedwongen om hun toevlucht te nemen tot deze impopulaire methode. De punt was in staal 8C, dat uitzette na afschrikken, en dit dwong de fabrieksarbeiders natuurlijk om het te snijden met branders op hoge temperatuur. Het punt van verharding van het pantser in het snijgebied was verloren.
Het is niet de moeite waard om te beweren dat de aanbevelingen voor het verbeteren van het productieproces alleen negatief waren voor de kwaliteit van het pantser. Dus een echte innovatie in de montage van de rompen van T-34-tanks was het lassen van pantserplaten "in een doorn" in plaats van het oude "in de sluis" en "in een kwart". Nu sneden de parende delen niet in elkaar, maar overlapten ze elkaar gedeeltelijk. Alleen door deze beslissing is het volume aan machine-uren per geval aanzienlijk teruggebracht van 198,9 naar 36.
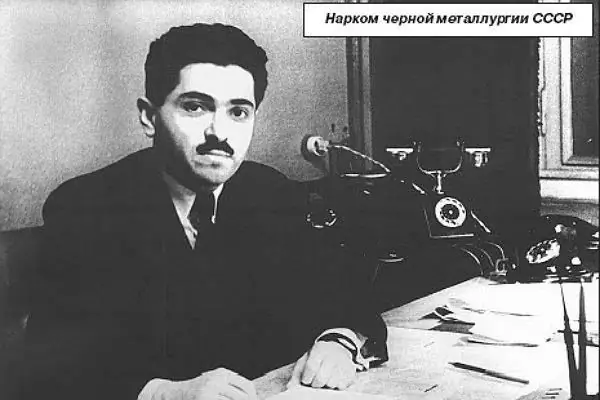
De belangrijkste leverancier van defecte staalplaat voor fabrieken die T-34 produceren, was de Novo-Tagil-fabriek van het Volkscommissariaat voor ferrometallurgie. Aanvankelijk werd hij onderbroken door bevoorrading van de fabriek in Mariupol en toen hij overstapte naar de zijne, kwam er een stroom klachten van het front en van de fabrieken. Met name in de samenstelling van het 8C-pantser van deze onderneming waren er ernstige discrepanties met de technische specificaties (TU) in het gehalte aan koolstof, fosfor en silicium. Over het algemeen waren er problemen met de TU. Het Volkscommissariaat van de ferrometallurgie was het er niet mee eens om de TU te behouden volgens de Mariupol-normen, waarin met name fosfor niet meer dan 0,035% mag zijn. Begin november 1941 keurde de Volkscommissaris van Ferrometallurgie Ivan Tevosyan nieuwe normen voor fosfor goed, waardoor het mogelijke gehalte werd verhoogd tot 0,04%, en van 4 april tot 0,045%. Opmerkelijk is dat historici het hier nog steeds niet over eens zijn, natuurlijk een belangrijke factor in de kwaliteit van pantserstaal. Nikita Melnikov vermeldt in het bijzonder dat de Novo-Tagil-fabriek integendeel medio 1942 het fosforaandeel verminderde van 0,029 % tot 0,024 %. Het lijkt erop dat verschillende wetenschappers verschillende redenen vinden voor het verschijnen van defecte T-34's aan de voorkant. Hoe het ook zij, de aangegeven normen voor het gehalte aan chemische elementen in de samenstelling van staal werden soms niet nageleefd. Het was voor de fabrieken moeilijk om een eenvoudige uniformiteit van de geleverde gewalste producten tot stand te brengen. Het parket onthulde ook dat bij de ondernemingen van ferrometallurgie in open haardovens, gepantserd staal "niet gaar" was - in plaats van 15-18 uur in werkelijkheid, niet meer dan 14 uur.
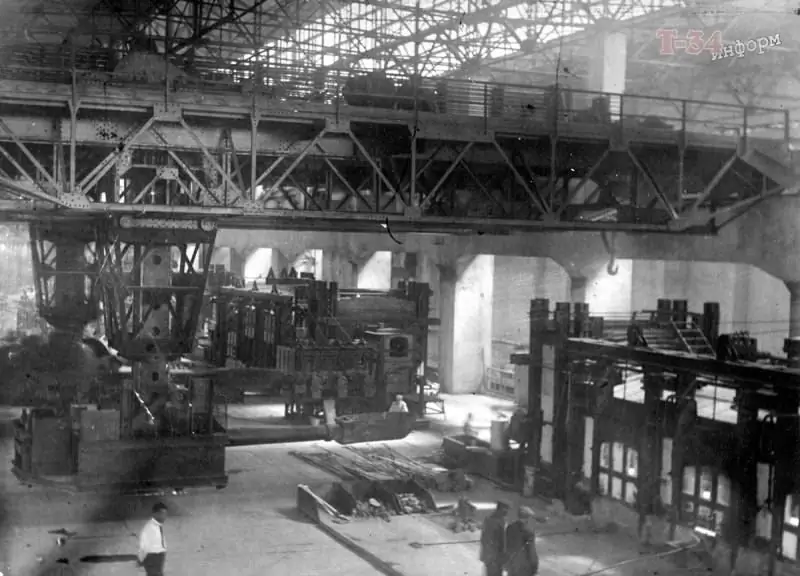
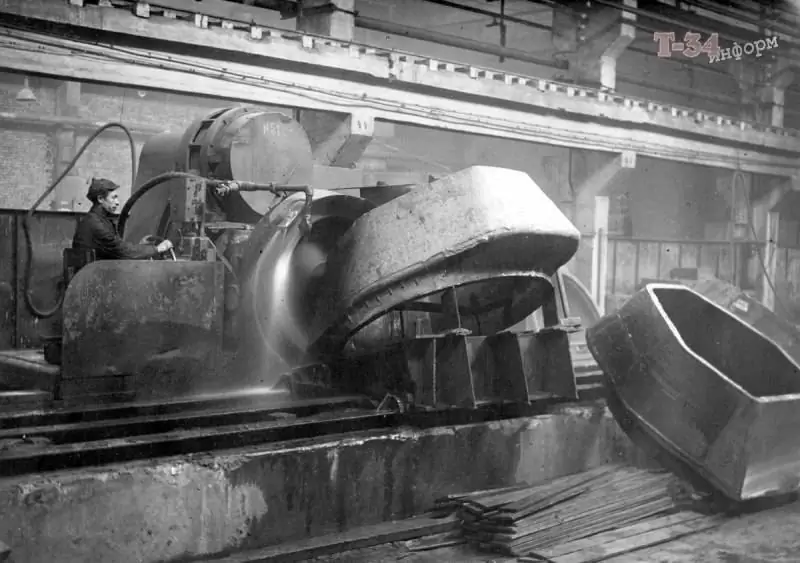
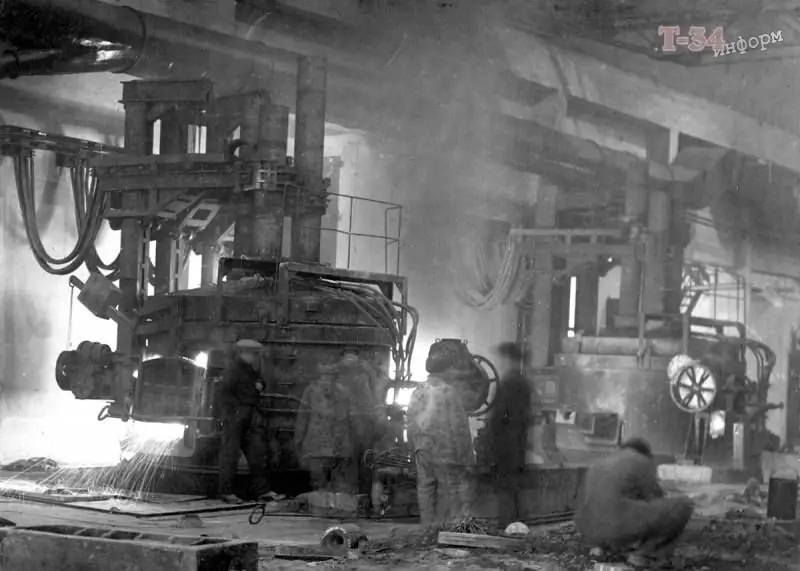
Toen informatie over de oorzaken van scheuren op de T-34-rompen Molotov bereikte, begonnen de volkscommissariaten van ferrometallurgie en de tankindustrie de verantwoordelijkheid op elkaar af te schuiven. Ten eerste was de belangrijkste reden het hoge gehalte aan fosfor in de pantserplaten, voor de andere ernstige schendingen van de rompproductietechnologie bij tankfabrieken.
Als gevolg hiervan was TsNII-48 betrokken bij het werk aan het bestrijden van scheuren op de T-34 (hoewel hij indirect schuldig was aan hun uiterlijk). Het pakket maatregelen dat het instituut pas eind 1943 had voorgesteld, maakte het mogelijk enkele opmerkingen weg te nemen. En de verbetering van de kwaliteit van de staalproductie bij ferrometallurgiebedrijven maakte het mogelijk om het aandeel afwijzingen te verminderen van 56, 25% in 1942 tot 13, 30% in 1945. De ondernemingen bereikten pas aan het einde van de oorlog het niveau van bijna 100%.